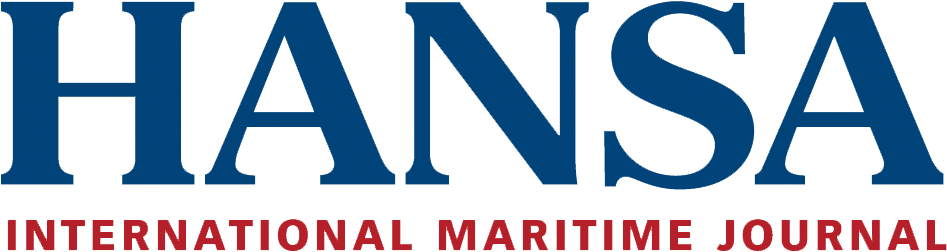
ADDITIVE FERTIGUNG IN DER MARITIMEN INDUSTRIE
Potenziale • Verfahren • Einsatz • Dienstleister
In Kooperation mit:
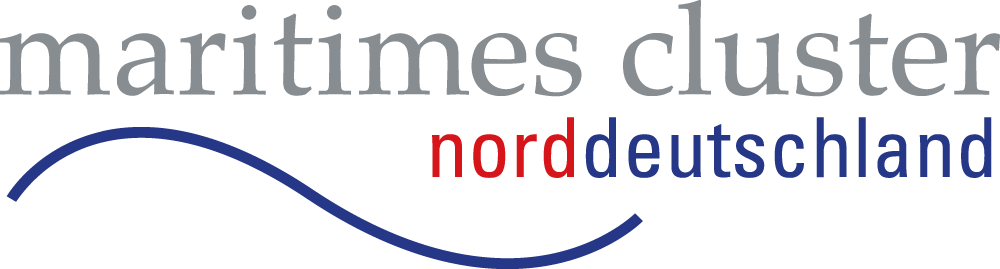
Welche Chancen bieten additive Fertigungsmethoden der maritimen Industrie? Welche Verfahren sind relevant und was sind die vielversprechendsten Einsatzszenarien? Was ist von der Vision vom 3D-Drucker für den Ersatzteildruck an Bord zu alten? Olaf Steinmeier, Leiter des IAPT Center Laser & Großstrukturen von der Fraunhofer-Einrichtung für Additive Produktionstechnologien (IAPT) spricht darüber im Video. Er ist einer der Autoren der STUDIE ZUR BEDARFSERMITTLUNG VON ADDITIVEN FERTIGUNGSMETHODEN MIT FOKUS AUF DIE MARITIME WIRTSCHAFT IN DER ERWEITERTEN METROPOLREGION HAMBURG für das Maritime Cluster Norddeutschland.
Können Sie sich das vorstellen, ein Propeller für ein Handelsschiff aus einem 3D-Drucker? Wie soll das gehen, und vor allem: Wie soll was gehen? Und mit wem und womit? Und mit welchen Folgen?
Diese und weitere Fragen beschäftigen uns, seitdem das Thema auch in der maritimen Industrie mehr und mehr Aufmerksamkeit bekommt, sei es nun entweder positiv-hoffend oder negativ-belächelnd. In Gesprächen mit Vertretern der Branche zeigte sich, dass wir nicht die Einzigen waren, denen sich das weite Feld der additiven Fertigung noch nicht in Gänze erschlossen hat – zumindest nicht bezüglich der Möglichkeiten und Schwierigkeiten für die maritime Industrie.
Bislang gegossen und/oder geschweißt, könnten in gar nicht so ferner Zukunft tatsächlich einige Elemente additiv gefertigt werden, das haben Viele erkannt. Kleines Beispiel: Der alteingesessene Deutsche Verband für – man achte auf den Namenszusatz – Schweißen und verwandte Verfahren (DVS) hat sich als Unterstützer der ersten Fachtagung »Additive Manufacturing« geoutet, die im November in Halle an der Saale stattfindet. Man ist überzeugt, dass der 3D-Druck heute schon häufiger in der industriellen Produktion eingesetzt werden kann, als dies in den Fertigungshallen praktisch der Fall ist, heißt es.
Andere Branchen wie die Luftfahrt und Medizintechnik gelten ohnehin als Vorreiter im 3D-Druck. Anders die maritime Industrie. Der Vergleich hinkt allerdings gewaltig, zu unterschiedlich sind Baugrößen, Anforderungen, Materialien, Märkte und Kosten.
Potenzial hat die Technologie aber auch in der Schifffahrt. Also haben wir uns näher damit beschäftigt. Und wir haben uns Partner gesucht, um einen umfassenden Überblick zu geben, den wir für dringend nötig halten. Diesen Partner haben wir im Maritimen Cluster Norddeutschland (MCN) beziehungsweise dessen Hamburger Niederlassung gefunden. Das war kein Zufall – das MCN hatte im Frühjahr die Ergebnisse einer bei der Fraunhofer-Einrichtung für Additive Produktionstechnologien IAPT in Bergedorf in Auftrag gegebenen Studie veröffentlicht. Darin geht es um eine sogenannte »Bedarfsermittlung« mit Fokus auf die maritime Industrie in der erweiterten Metropolregion Hamburg.
Herausgekommen ist dieser erste – nach jetzigem Stand sicher nicht letzte – Report der HANSA. »Drucken« ist seit jeher Teil unseres Geschäfts, auch wenn wir uns mit Blick auf unser Portal www.hansa-online.de nur sehr ungern darauf reduziert sehen. Unsere »3D-Druck«-Publikation ist daher auch cross-medial angelegt. Neben Berichten und Bildern »print« gibt es online weitere Informationen, Videos und Einordnungen dort, nicht zu vergessen Einblicke, Rückblicke und Ausblicke. Ein Blick lohnt sich – versprochen.
Es geht um Einblicke und Überblicke. Einblicke in Potenziale für verschiedene Einsatzgebiete, mögliche Effekte auf verschiedene Geschäftsbereiche in der maritimen Branche. Überblicke über die Palette an 3D-Druckverfahren und Dienstleister, die entweder bereits im »Maritimen« aktiv sind oder Partner sein könnten. Nicht zuletzt geht es auch um Initiativen innerhalb der Branche, den 3D-Druck ökonomisch und regulatorisch stärker zu etablieren.
Der Tenor war, ist und bleibt: Für eine breite Anwendung sind die technische Machbarkeit und die wirtschaftliche Sinnhaftigkeit elementar. Dabei geht es nicht zuletzt um Vorteile und Nachteile. Vorteile sind die »unbegrenzte gestalterische Freiheit«, Möglichkeiten des Leichtbaus und die Integration mehrerer, vormals einzelner Bauteile. Dazu gehören kürzere Logistik-Ketten, Sensorik-Optimierungen und Qualitätsverbesserungen in puncto Festigkeit, Porösität oder Funktionalität. Dafür geeignet sind nicht nur der oft als Beispiel angebrachte gedruckte Propeller, sondern auch die Antriebstechnik und der Schiffsbetrieb. Nachteile wiederum können Größenbeschränkungen, Kosten und die Genauigkeit sein. Man merkt schnell, es besteht Klärungsbedarf.
Als besondere Empfehlung legen wir Ihnen ein Video-Interview ans Herz, das wir mit Olaf Steinmeier vom IAPT geführt haben. Der ausgewiesene Experte erläutert die Potenziale vom 3D-Druck in Schifffahrt, Schiffbau und Häfen. Auch der Ersatz von bisherigen Metallteilen durch Kunststoff ist für ihn mit Blick auf ein aktuelles Forschungsprojekt kein Tabu.
Allerdings macht er auch deutlich, was wir in vielen Gesprächen mit den Unternehmen gehört haben, die im 3D-Druck aktiv sind oder werden wollen:
Es ist enorm wichtig, dass die additive Fertigung als Standardverfahren etabliert und von Klassifikationsgesellschaften akzeptiert wird, ansonsten muss jedes Bauteil einzeln zertifiziert werden. Man müsse allgemeine Richtlinien entwickeln, so dass keiner mehr fragt, ob ein additiv gefertigtes Bauteil die selben Anforderungen erfüllen kann wie ein Gegossenes.
Der maritimen Industrie ist zu wüschen, dass sie auf die vielen offenen Fragen zur Anwendung von additiver Fertigung Antworten findet.
Im Idealfall hätten wir damit »Futter« für eine neue Veröffentlichung, ein Update mit neuen Praxisbeispielen und wichtigen Erfahrungswerten. Wir bleiben auf jeden Fall dran. (MM)
Wird über die industrielle Zukunft debattiert, wird neben allgemeinen Schlagworten wie Digitalisierung und Industrie 4.0. immer häufiger eine viel konkretere Technologie genannt: der 3D-Druck. Das gilt auch für die maritime Industrie.
Experten verweisen dann nicht selten darauf, dass diese Technologie gar nicht mehr so neu ist. Additive Fertigungsverfahren, wie der 3D-Druck, sind in vielen Industriebereichen bereits weit verbreitet. Allerdings gilt die weite Welt der Schifffahrt bislang nicht gerade als Vorreiter in der praktischen Umsetzung. Das liegt auch daran, dass die Möglichkeiten den beteiligten Akteuren oft gar nicht richtig bekannt sind – und schon gar nicht nicht genutzt werden. In der Regel sind selbst die bereits aktiven Dienstleister unbekannt.
Das Maritime Cluster Norddeutschland will dem Einsatz von 3D-Druck Schub verleihen. Im Jahresverlauf war dafür eine Studie »Bedarfsermittlung von additiven Fertigungsmethoden mit Fokus auf die maritime Wirtschaft in der erweiterten Metropolregion Hamburg« veröffentlicht worden, die das MCN bei der in Hamburg-Bergedorf ansässige Fraunhofer-Einrichtung für Additive Produktionstechnologien (IAPT) in Auftrag gegeben hatte. Die Ergebnisse sind durchaus beachtlich.
Denn auch in der Schifffahrt ist ein Wandel von der Massenfertigung hin zur flexiblen, individuellen Fertigung zu beobachten. Additive Fertigung ist ein Teil davon. Dabei werden Bauteile durch schichtweisen Auftrag von Material aus einem formlosen Rohstoff, wie beispielsweise Metallpulver, generiert. Im Gegensatz zu konventionellen Fertigungsverfahren wie Drehen, Fräsen oder Gießen, erlauben additive Fertigungsverfahren die wirtschaftliche Herstellung komplexer, organischer Strukturen in kleinen Stückzahlen bis hin zur Losgröße 1.
Übertrag auf maritime Industrie
Die Studie erläutert Anwendungen von additiver Fertigung. Dies umfasst unter anderem verfügbare Technologien. Durch die konstruktiven Gestaltungsfreiheiten, die sich mit additiver Fertigung realisieren lassen, bieten sich aus Produktsicht Leichtbaumöglichkeiten, Funktionsintegrationspotenziale, Individualisierungsmöglichkeiten sowie die generelle Chance, die Produktqualität zu steigern, heißt es. Aus Prozesssicht bietet sich eine Kostenreduktion im Hinblick auf die Fertigung oder den gesamten Lebenszyklus des Produktes. Eine Materialeffizienzsteigerung sowie eine Verringerung der Produkteinführungs- bzw. Produktbereitstellungszeit seien weitere prozessseitige Potenziale.
Die branchenübergreifend aufgezeigten Potenziale werden sodann auf die maritime Branche übertragen. Neben den allgemeingültigen Anwendungsbereichen Prototypenbau und Ersatzteilbereitstellung gibt es verschiedene Unternehmenskategorien mit maritimem Bezug, die Anwendungspotenziale für additive Fertigung bieten. Hierzu werden beispielsweise Werften beim Formenbau gezählt, Zulieferer für Schiffsantriebstechnik bei Motoren und Getrieben, Zulieferer für Manövrier- und Antriebssysteme bei Antriebssträngen und Propellern, Zulieferer für Schiffsbetriebsanlagen bei Wärme-, Pumpen- und Hydrauliksystemen sowie Unternehmen der Meerestechnik bei Spezialequipment.
Es folgt eine praktische Bauteilanalyse bei Unternehmen aus der maritimen Wirtschaft. Sie belegt nach Ansicht des IAPT »das Vorhandensein eines breit gestreuten Anwendungspotenzials«. Am häufigsten tritt ein Nutzen für die untersuchten Unternehmen durch additiv gefertigte Ersatzteile auf, insbesondere in der Substitution von defekten Gusskomponenten.
Bei großen Bauteilen bietet sich demnach zudem eine auf additiven Verfahren basierende Reparaturlösung an. Freiformflächen, wie sie an Bootsrümpfen oder auch an strömungsbehafteten Komponenten größerer Schiffe zu finden sind, bilden ebenfalls ein geeignetes Anwendungsfeld für den 3D-Druck, aus wirtschaftlichen Gründen bisher bevorzugt unter Verarbeitung von Kunststoffen.
Besonderes Potenzial liefert schließlich generell der Bereich der Meerestechnik, da die dort benötigten Komponenten hohe funktionale Anforderungen erfüllen müssen, die mit Hilfe der additiven Technologien besser erfüllt werden können.
Im zweiten Kapitel wird eine Übersicht gegeben, welche Dienstleister es für additive Fertigung in Deutschland und insbesondere im Einzugsgebiet des MCN bereits gibt. Bei diesen Dienstleistern handelt es sich um potenzielle Kooperationspartner, mit denen Projekte mit additiver Fertigung initiiert oder abgewickelt werden können. Dienstleister bieten neben der eigentlichen Lohnfertigung in der Regel auch vorgelagerte Services wie 3D-Scanning oder Konstruktion sowie nachgelagerte Services wie Oberflächenveredelung und Qualitätssicherung an. Diese Services spiegeln nach Ansicht der Studien-Verfasser die gesamte Prozesskette von additiver Fertigung wider.
Ein signifikanter Anteil der deutschlandweit identifizierten Dienstleister ist im Einzugsgebiet des MCN ansässig, »so dass eine regionale Abdeckung für potenzielle Anwender sichergestellt ist«.
»Aufgrund der starken Verbreitung des 3D-Drucks in anderen Industriebereichen kann die maritime Industrie ressourcenschonend an das Thema herangehen – es müssen keine gänzlich neuen Wege gegangen werden und das Risiko in der Nutzung dieser neuen Technologie kann so für neue Anwender verringert werden«, sagt dazu Lina Harms, Leiterin der MCN-Geschäftstelle Hamburg.
Im dritten Kapitel wird die Implementierung von additiver Fertigung in Industrieunternehmen mit Fokus auf KMU betrachtet. Einerseits werden die aktuellen Hemmnisse untersucht, die den Implementierungsprozess von additiver Fertigung in einem Unternehmen behindern können. Es kristallisieren sich vier zentrale Herausforderungen heraus: technologischer Reifegrad, Personalqualifizierung, Kosten sowie mangelnde Prozessregularien.
»Weniger Hemmnisse zu erwarten«
Es sei jedoch in den nächsten ein bis fünf Jahren mit einem deutlichen Abbau dieser Hemmnisse zu rechnen, allein schon im Zuge einer voranschreitenden Industrialisierung der additiven Fertigung.
Anhand von konkreten Best-Practice-Beispielen wird die erfolgreiche Implementierung von additiver Fertigung dargestellt. Am Beispiel zweier Unternehmen mit weniger als 25 Mitarbeitern wird der Verlauf von der initialen Idee bis hin zur vollständigen Implementierung von additiver Fertigung in der Serie aufgezeigt. »Beide Beispiele verdeutlichen, dass eine Implementierung einer neuen Technologie, wie additiver Fertigung, ein sukzessiver Prozess ist«, wird deutlich gemacht.
Zu Beginn steht der Knowhow-Aufbau bei den Mitarbeitern im Fokus. In diesem Anfangsstadium wird auf die Unterstützung von Entwicklungsdienstleistern und Lohnfertigern zurückgegriffen. Sobald Projekte mit additiver Fertigung in einer gewissen Regelmäßigkeit abgewickelt werden, gilt es, die Investition in eine eigene additive Fertigungsinfrastruktur zu überprüfen.
Die 3D-Studie ist veröffentlicht, das Echo war nicht unerheblich. An ein »Abwarten« denkt man beim Maritimen Cluster Norddeutschland (MCN) nun keineswegs.
Auch künftig wird das Thema »additive manufacturing« (AM) weiter vorangetrieben, fokussiert vor allem in der Geschäftsstelle Hamburg. Die Planung für weitere Aktivitäten laufen dem Vernehmen nach auf Hochtouren. Die Hamburger Hochschule für angewandte Wissenschaften (HAW) spielt dabei eine nicht unerhebliche Rolle. Sie ist Mitglied im MCN und bereits jetzt sehr aktiv im Bereich 3D-Druck. Entsprechend gibt es regen Austausch zwischen dem MCN und der HAW – in Person von Prof. Dr. Sharam Sheikhi von der Fakultät Technik und Informatik beziehungsweise dem Department Maschinenbau und Produktion.
Sheikhi ist Professor für Werkstoffkunde und Fügetechnik und gilt als ausgewiesener Experte. Gemeinsam mit der HAW, die dem MCN fachlich beratend zur Seite steht, werden die weiteren Aktivitäten geplant und fachlich abgestimmt.
Zudem will eine Gruppe von rund 20 Unternehmen im Bereich 3D-Druck für die maritime Wirtschaft zusammenarbeiten. Die Gruppe wurde maßgeblich durch das MCN zusammengebracht und koordiniert. Bis Ende Oktober 2019 soll ein Vollantrag für die ZIM-Kooperationsnetzwerkförderung gestellt werden. Bei Redaktionsschluss dieser Publikation waren die Vorbereitungen in vollem Gange.
Sollte die Projektförderung zugesagt werden, sollen aus diesem Netzwerk heraus spannende Forschungs- , Dienstleistungs- und Entwicklungsprojekte bereits im Jahr 2020 gestartet werden. Zu den wahrscheinlich aufgegriffenen Themen zählen u.a. Lösungsentwicklungen für größere Bauraumbeschränkungen verschiedener AM-Verfahren, ein Projekt zur Oberflächenbeschaffenheit, ein Projekt zum Thema Sensorik, sowie Projekte zum Thema Werkstoffe.
Wichtig ist den Verantwortlichen im MCN zudem eine gewisse öffentliche Aufmerksamkeit, damit Potenziale in der maritimen Industrie benannt, erkannt und schlussendlich gehoben werden können. Workshops sollen weitergeführt, die Zusammenarbeit mit weiteren Akteuren aus der AM-Branche intensiviert werden.
Nicht zuletzt soll auch die Schiffbau-Leitmesse SMM erneut als Plattform genutzt werden, sie findet im September 2020 wie gewohnt in Hamburg statt.
Das Maritime Cluster Norddeutschland (MCN) hatte den 3D-Druck in der maritimen Industrie im Rahmen der Schiffbau-Leitmesse SMM 2018 erstmals einer breiten Öffentlichkeit veranschaulicht und damit für großes Aufsehen gesorgt. Bei der nächsten SMM 2020 in Hamburg wird es eine Neuauflage geben.
So wird es erneut eine große Sonderschau zur additiven Fertigung geben. Als Ausstellungsfläche konnte sich das MCN rund 100m² sichern, die mit fünf bis acht Ausstellern besetzt sein werden – nach aktuellem Stand unter Umständen auch mit internationalen Ausstellern.
Das Konzept beinhaltet wieder eine »Show Arena«, wo es »3D-Druck zum Anfassen« am Stand geben wird. Für Messe-Besucher und Interessierte plant das SMM einen Strauß an Aktivitäten, um das Spektrum und die Potenziale der Technologie für die Branche aufzuzeigen. So wird es erneut Live-Vorführungen von 3D-Druck geben, und zwar in verschiedenen Verfahrenstechniken. Neben einer Ausstellung von »realen maritimen Bauteilen« soll zudem die Entstehungsgeschichte von 3D-gedruckten Bauteilen präsentiert werden: vom Engineering und der Erstellung der CAD-Zeichnungen über den eigentlichen physischen Druck über die Nachbearbeitung der Bauteile bis hin zu ihrer Prüfung und Zertifizierung. Zu jedem Thema werden entsprechende Unternehmen als Unteraussteller am Stand vor Ort sein. Nicht zuletzt runden Fachvorträge das Angebot am Messe-Stand ab.
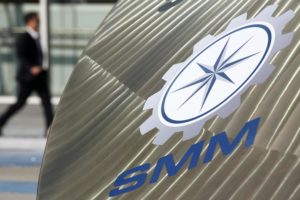
2018 hatte es erstmals die »Maritime 3D Printing Show Area« mit Live-Vorführungen, Vorträgen und Ausstellern aus dem Bereich der additiven Fertigung gegeben. Das MCN hatte die Sonderschau gemeinsam mit der Hamburg Messe und Congress (HMC) geplant. Zu den Ausstellern gehörten seinerzeit die MCN-Mitglieder MMG Mecklenburger Metallguss, Rolf Lenk Werkzeug u. Maschinenbau und TREO – Labor für Umweltsimulation.
Die Aktion folgte auf die im August 2017 veröffentlichte Studie »Perspektiven des 3D-Drucks für die maritime Wirtschaft in Norddeutschland« sowie mehreren MCN-Workshops.
Auf der SMM 2020 wird auch die Hochschule für angewandte Wissenschaft (HAW) Hamburg live 3D-Schweißverfahren demonstrieren. Prof. Sharan Sheikhi von Institut für Werkstoffkunde und Schweißtechnik an der HAW ist der Experte, wenn es um Auftragschweißen geht. Er erforscht, wie man die Technik besser, reifer machen kann. Sheikhi will beispielsweise Konstruktion und Schweißtechnik zusammenbringen. Ihm schwebt eine universelle Schnittstelle für die CAD-Systeme und Schweißmaschinen vor, bei der solche Faktoren schon eingerechnet sind und die automatisch die Zeichnung für den Roboter übersetzt. Denn Metall verhält sich anders als Kunststoff, was beispielsweise die Wärmeableitung angeht. Zwar können Metallstrukturen nach einer digitalen Konstruktionszeichnung »gedruckt« werden, das heiße Metall kann die Struktur aber auch wieder zerstören.
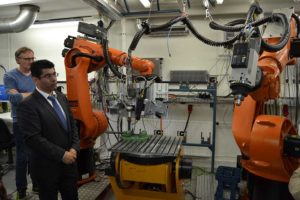
Auch die Oberflächennachbearbeitung erforscht Sheikhi als teil des Schweißprozesses. Als problematisch erweisen sich teils noch die rauen Oberflächen, die sowohl Pulver- als auch Draht-basierte Verfahren hinterlassen. Bei rauen Oberflächen bestehen mehr Risiken für die Rissbildung als bei glatten. Bei Schiffspropellern oder Turbinenschaufeln ist eine fräsende Nachbearbeitung der Oberflächen möglich (wie sie auch bei Gussteilen nötig ist). Ein nachträglich Fräsen oder Zerspanen von Hinterschneidungen oder Hohlräumen in Bauteilen ist derzeit aber kaum möglich. Teilweise können zwar Schleifflüssigkeiten durch die Kanäle gepresst werden, das ist aber nicht für alle Anwendungsfälle eine Lösung. Daher arbeitet Sheikhi mit seinem Team an einem Roboter-Tandem: Der eine Roboterarm schweißt eine oder mehrere Lagen Material auf, ein zweiter Arm fräst dann die Unebenheiten weg. So sollen sie sich Schicht um Schicht vorarbeiten. Außerdem soll es im kommenden Jahr ein Laser-Coaxialsystem geben, bei dem der Schweißdraht durch den Laserkopf hindurch geführt wird. So besteht keine Richtungsabhängigkeit mehr beim Schweißen. Man darf also gespannt sein, was 2020 in der Show-Area auch an Forschritten gegenüber heute geboten wird.
Bei MCN hat man jedenfalls ein klares Ziel: Die Leute sollen nicht dazu bewegt werden, bekannte Bauteile von nun an additiv zu fertigen, anstatt sie zu gießen oder zu fräsen. Vielmehr will man dazu anregen, ganz neu über die Bauteile nachzudenken.
Handlungsempfehlungen zur kurz-, mittel- und langfristigen Auswahl von additiven Fertigungstechnologien
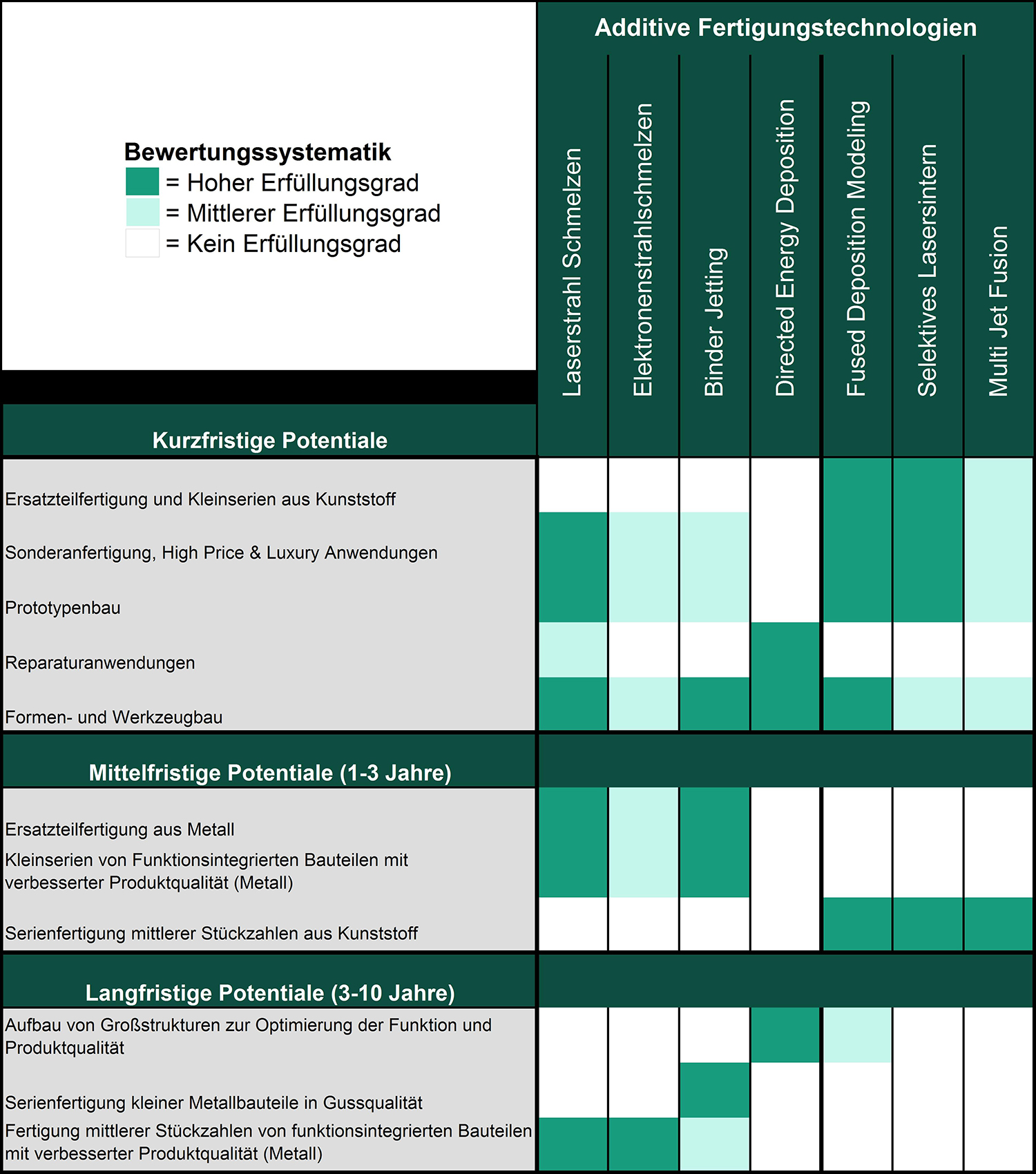
Korrelation von Anwendungsbeispielen nach Kategorie und Potentialen der additiven Fertigung
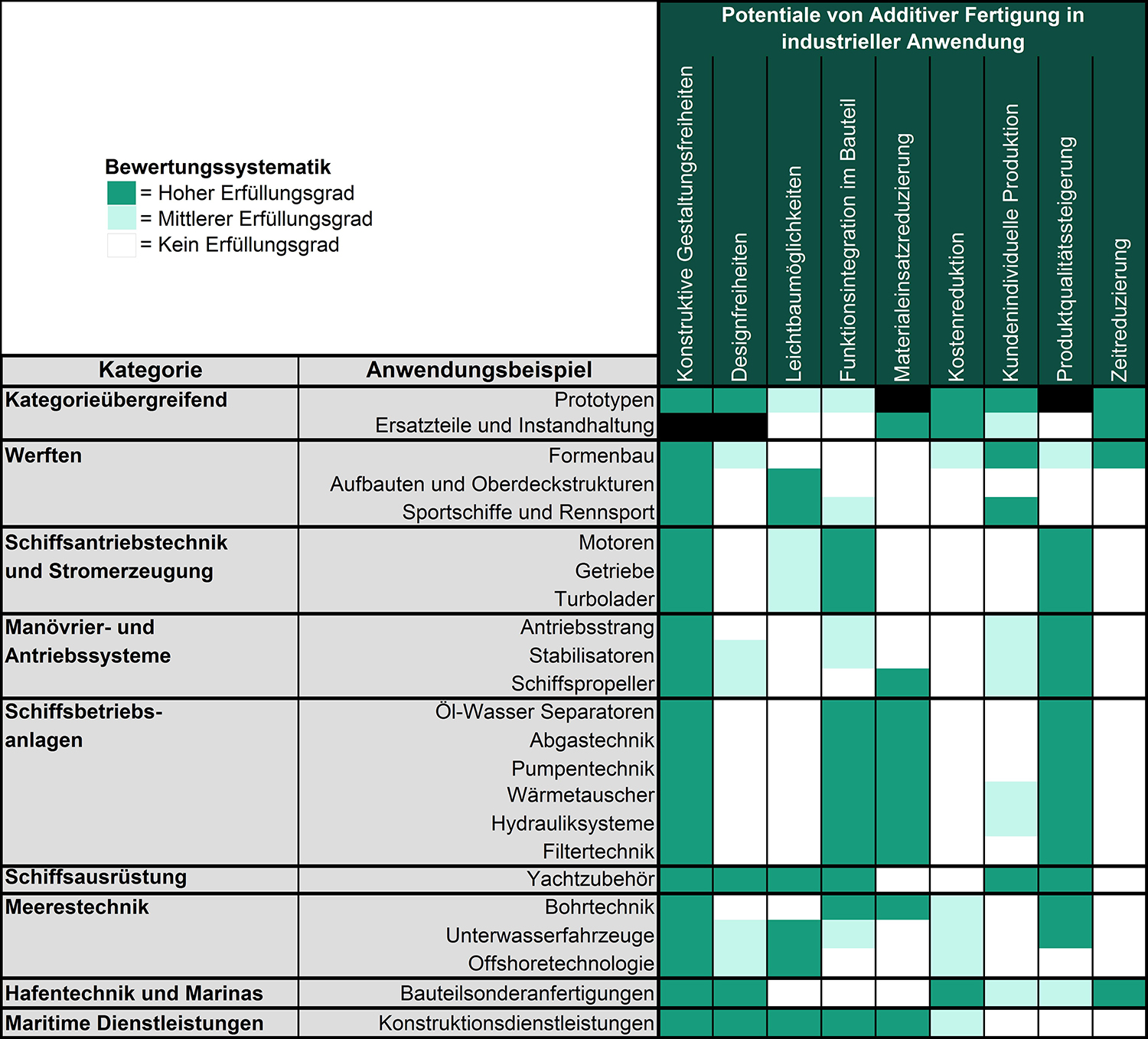
Quelle: Studie zur Bedarfsermittlung von additiven Fertigungsmethoden mit Fokus auf die Maritime Wirtschaft in der Erweiterten Metropolregion Hamburg
Metall-additive Fertigung
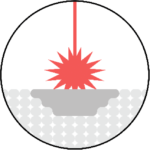
Die am weitesten verbreitete und reifste metallverarbeitende Technologie ist nach Ansicht der IAPT-Experten das Laserstrahlschmelzen (LBM von Laser Beam Melting). Es gibt bereits einige Serien-Anwendungen, vor allem in der Luftfahrt und der Medizintechnik. Branchen wie der Maschinenbau oder die Automobilindustrie fertigen bereits Kleinserien und Einzelteile. Auch für Ersatzteile existieren Anwendungen etwa in der Schienenfahrzeugindustrie. Allerdings, so die Einschränkung, für eine breitere Anwendung der Technologie müssen insbesondere die Bauteilkosten weiter sinken und die Qualifizierbarkeit der Prozesskette erleichtert werden.
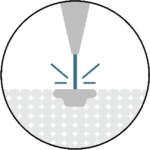
Das pulverbettbasierte Elektronenstrahlschmelzen (Electron Beam Melting) wid als Ergänzung betrachtet. Die Lenkung des Elektronenstrahls mit Hilfe von Spulen ermöglicht eine schnellere Baugeschwindigkeit. Außerdem treten kaum Eigenspannungen auf, weswegen das Verfahren sich in erster Linie für massive, komplexe Titanbauteile eignet. Zum jetzigen Zeitpunkt ist diese Methode allerdings nur für Nischen eine Option, da die eingeschränkte Materialvielfalt (Titan und Kobalt-Chrom), die komplexe Prozesssteuerung und eingeschränkte Bauraumgröße Restriktionen sind.
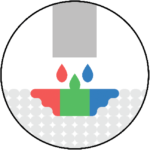
Das auf der Sintertechnologie basierende Pulverbettverfahren Binder Jetting gilt beim IAPT als »aufstrebendes« Verfahren. Durch Verfahrensinnovationen soll in den nächsten Jahren die Produktivität additiver Fertigungsverfahren sprunghaft um ein vielfaches erhöht werden. Für das Verfahren spricht zudem, dass günstige Sinterpulver (MIM) als Ausgangswerkstoff verwendet werden. Bis auf Aluminium, das sich nicht sintern lässt, sind gängige Werkstoffe verwendbar. Eine Beschränkung seien jedoch Bauteileigenschaften und der Umstand, dass das Sintern nur für kleine Bauteile möglich ist. Heute findet das Binder Jetting vorwiegend Anwendung bei der Herstellung von Werkzeugen. Das könnte sich jedoch bald ändern, wegen der Skalierbarkeit und des Kostensparpotenzials wird bereits die Serienfertigung beispielsweise in der Automobilindustrie erprobt. Bei der Herstellung von Sandguss Formen bis zu 4 x 2 x 1 m kann ein Sonderprozess des Binder Jetting angewendet werden. Hier wird anstelle eines Metalls Sand mit Hilfe eines Harzes gebunden.
Eine ähnliche Technologiegruppe sind die Metal-Fused-Deposition Verfahren, bei denen der metallische Werkstoff mit einem Kunststoff gebunden wird. Die Anlage ist zwar günstiger, allerdings schränkt der zweistufige Sinterprozess die Bauteilgröße ein.
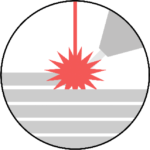
Die DED-Technologien basieren auf dem klassischen Auftragsschweißen. Auf diese Weise können auch sehr große Strukturen aufgebaut werden, je nachdem wie groß die Reichweite der Maschinen ist, etwa von Portal-Maschinen oder Robotern. Als Vorteil gelten die deutlich niedrigeren Bauteilkosten und die um ein vielfaches schnellere Aufbaurate ist. Ein Nachteil liegt in der erreichbaren Bauteilkomplexität, »da ein Support von Überhängen nicht zielführend ist«, so das IAPT. Zudem muss die produzierte Oberfläche in aller Regel nachbearbeitet, also nachzerspant werden.
Mit diesem Verfahren werden häufig schwer zu zerspanende Materialien, wie Titan oder Inconel verarbeitet. So soll Werkzeugverschleiß eingespart werden, da die Fertigung werkzeuglos erfolgt. Zu den etablierten Anwendungen gehören der Werkzeugbau, die Beschichtung und die Reparatur von Verschleißstellen.
DED umfasst verschiedene Prozesse mit verschiedenen Wirkprinzipien. Auf Grund der höheren Produktivität und der räumlichen Skalierbarkeit bergen die DED-Verfahren Zukunftspotential für die additive Herstellung von großen Metall-Strukturen, wie sie in maritimen Anwendungen häufig zu finden sind, heißt es in der Studie.
Die lichtbogenbasierten Verfahren (WAAM, Wire Arc Additive Manufacturing) zeichnen sich durch geringe Anlagenkosten und den schnellen Aufbau großer, grober Strukturen aus. Als Ausgangswerkstoffe sind alle schweißbaren Materialien anwendbar. Einschränkungen ergeben sich aus der Verwendung eines Drahtes. Spröde Materialien, wie Hartmetalle oder Stellite Legierungen, lassen sich nicht zu einem Draht verarbeiten.
Die Anwendungen, die dem laserbasierten Verfahren (LMD, Laser Metal Deposition) gefertigt werden, sind eher kleiner, der Vorteil liegt darin, dass sich vergleichsweise feinere Strukturen fertigen lassen. Auch Pulver kann als Ausgangmaterial genutzt werden. So stehen auch spröde Materialien zur Verfügung, es lassen sich komplexere Strukturen darstellen. Darüber hinaus existieren weitere DED-Verfahren wie Rührreibschweißen oder Elektronenstrahlschweißen.
Kunststoff-additive Fertigung
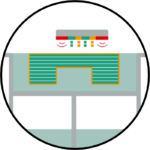
Die auf dem Binderprinzip aufbauende, neue MJF-Technologie nimmt einen zunehmend höheren Stellenwert bei der additiven Fertigung von Kunststoffen ein. Es ähnelt von den Bauteileigenschaften und verwendbaren Werkstoff (PA 12, PA 11) dem Selektiven Lasersintern. Der Vorteil liegt in prinzipiell schnelleren Bauzeiten und geringerer Bauteilkosten. Die Skalierbarkeit der Prozesskette und die »Industrie 4.0«-Fähigkeiten des Verfahrens sollen eine individualisierte Produktion großer Stückzahlen ermöglichen.
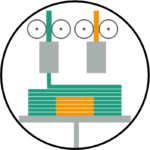
Nicht zuletzt aufgrund des relativ geringen Preises für einige Geräte eignet sich das düsenbasierte Verfahren FDM – bekannt auch aus dem Hobbybereich – sehr gut für den Einstieg in die additive Fertigung oder den Prototypenbau und Montagehilfen. In der Industrie gibt es Anwendungen für größere Kunststoffteile und kleine Serien.
Die Reedereigruppe Maersk hat in der Vergangenheit im FDM-Verfahren einfache Ersatzteile an Bord gedruckt. Das war zwar erfolgreich, prinzipiell ist das Verfahren vor allem für relativ einfache Bauteile eine Option.
Als Vorteil gilt die breite Materialpalette, die leistungsfähige Materialien enthält (PEK, PEI, PEKK, ASA, PC, PETG). Haupteinschränkung seien die begrenzten Materialeigenschaften, »die durch eine deutliche Anisotropie gekennzeichnet sind«, schreibt die Fraunhofer-Einrichtung. Dank temperaturbeständigen, nicht-brennbaren PEI-Werkstoff ergeben sich auch Anwendungen in kritischen Bereichen.
Auch in der maritimen Industrie findet dieses Verfahren bereits Anwendung, ein Beispiel ist das in Waren an der Müritz ansässige Unternehmen Mecklenburger Megallguss MMG. Die neueste Maschine im Portfolio von XXL Metalworking Services ist ein Kunststoff-3D-Drucker. Laut MMG gehört er mit einem Bauraum von ca. 2.000 x 2.000 x 2.000mm zu den größten 3D-Druckern in der maritimen Industrie. Möglich sind etwa der Druck – verwendet wird der Werkstoff PLA – von Gussmodellen oder auch großen Konstruktionsbauteilen.
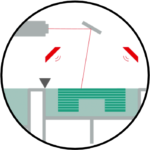
Für die additive Fertigung von Kunststoffen ist laut dem IAPT das pulverbettbasierte SLS die am weitesten verbreitete Technologie – nicht zuletzt aufgrund guter mechanischer Festigkeitswerte, sehr hoher Designfreiheit sowie der Verfügbarkeit des leistungsfähigen PA12-Werkstoffes.
Einer flächendeckenden Verbreitung stehen jedoch bislang vor allem die limitierte Auswahl an Materialien (PA 12, PA 11) sowie die im Verhältnis zum Spritzguss höheren Stückkosten bei großen Serien entgegen. Anwendung findet das Verfahren in der Kleinserienproduktion. Boeing nutzt zudem SLS, um komplexe Lüftungskanalstrukturen unter Einhaltung kurzer Lieferzeiten in einem Schritt herzustellen. Durch dessen hohe Flexibilität gilt SLS als beliebtes Verfahren zur Ersatzteilfertigung und im Prototypenbau in allen Branchen.
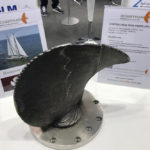
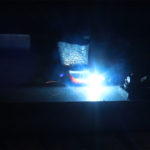
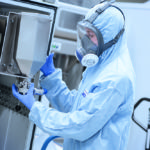
3D-Druck & Ersatzteilversorgung – Ein Potenzial wartet auf seine Erschließung
Der größte Vorteil der additiven Fertigung besteht darin, dass infolge maximaler Gestaltungsfreiheit auch geometrisch komplexe Strukturen relativ einfach schichtweise aufgebaut werden können.
Als Nutzen ergibt sich beispielsweise eine optimierte Bauteilfunktion durch besonders strömungsgünstig ausgeprägte Freiformflächen oder eine materialeffiziente und ressourcenschonende bionische Leichtbaukonstruktion.
Da für den additiven Herstellprozess keine speziellen Werkzeuge oder Formen benötigt werden, kann der 3D-Druck direkt und mit nur geringem Programmieraufwand aus den digitalen Bauteildaten heraus erfolgen. Demnach ist die additive Fertigung prädestiniert, um Bauteile »on demand« zu produzieren und diese neue Technologie in das Beschaffungsmanagement von Ersatzteilen einzubinden. Vorausgesetzt sind lediglich ein CAD-Modell des fehlenden Bauteils sowie ein 3D-Drucker und das zugehörige Know-how.
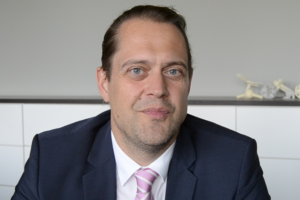
Ein Seitenblick zeigt, Schienenfahrzeughersteller und Bahnbetreiber haben bereits zahlreiche wirtschaftlich interessante Anwendungsbeispiele identifiziert und umgesetzt. Im Obsoleszenzfall wird das Ersatzteil aus Kunststoff oder aus Metall kurzerhand gedruckt, auf Lagerhaltung von Ersatzteilen oder von bauteilbezogenen Werkzeugen kann verzichtet werden. Mit Hilfe des 3D-Drucks steigt die Verfügbarkeit von Ersatzteilen. Und jeder Tag zählt!
Je früher ein Schienenfahrzeug wieder instand gesetzt und in Verkehr gebracht werden kann, desto geringer sind die Ausfallkosten bezogen auf das Gesamtsystem.
Dieses Szenario lässt sich auch auf den maritimen Einsatz übertragen. Im Schiffsbetrieb, aber auch im Bereich der Werft- oder Hafeninfrastruktur werden häufig Ersatzteile benötigt. Insbesondere Gussteile bedeuten einen hohen Aufwand, wenn sie in geringer Losgröße nachgefertigt werden müssen, und sie sind oft mit langen Lieferzeiten verbunden. Damit grundsätzlich die wirtschaftliche Sinnhaftigkeit des 3D-Drucks gegeben ist, sollte das potenziell betrachtete Bauteil eine gewisse geometrische Komplexität aufweisen, um die Herstellkosten für den Druck zu rechtfertigen. Normteile, einfache Bolzen oder Blechkonstruktionen mit ebenen Oberflächen sind dagegen für die additive Fertigung ungeeignet, da sie sich mit konventionellen Methoden wesentlich kostengünstiger herstellen lassen.
Allerdings kann die additive Fertigung einen zusätzlichen Mehrwert bieten, der in jeder Kalkulation berücksichtigt werden sollte. So besteht mittels 3D-Druck immer prinzipiell die Möglichkeit des Partialersatzes, sodass bei Bedarf nur einzelne Komponenten einer Baugruppe hergestellt und ausgetauscht werden müssen, auch wenn die Baugruppe beim ursprünglichen Lieferanten nur komplett erhältlich ist. Umgekehrt erlaubt es das Verfahren situativ auch, mehrere Einzelkomponenten zu einem additiv gefertigten Bauteil zusammenzufassen, um den Montageaufwand zu reduzieren. Treten konkrete Schwachstellen an einem Bauteil auf, lassen sich diese ohne größeren Aufwand durch ein Re-Design eliminieren, indem z.B. seine Wandstärke lokal etwas dicker ausgeführt wird. Nicht zuletzt kann das 3D-Druckverfahren genutzt werden, um sogenannte »Homecomer« zu erzeugen, die provisorisch die Funktion eines Bauteils solange übernehmen, bis ein Originalteil verfügbar ist.
Als bisherige Hemmnisse standen die Größenbeschränkungen für Bauteile, resultierend aus den Bauraumabmessungen der 3D-Druckanlagen, die vergleichsweise geringen Aufbauraten und die damit verbundenen hohen Fertigungskosten einer flächendeckenden Verbreitung der Technologie im maritimen Sektor entgegen. Diese Restriktionen verlieren jedoch zunehmend an Bedeutung.
Die 3D-Drucker wachsen, Aufbauraten steigen und neue Verfahren senken Bearbeitungszeit und –kosten. Hybride Strukturen, in denen additiv Schichten auf konventionell gefertigten Basiselementen aufgebaut werden, helfen ebenfalls, die Wirtschaftlichkeit insgesamt zu verbessern, weil das gedruckte Bauteilvolumen abnimmt und nur diejenigen Bereiche eines Bauteils gedruckt werden, für die der 3D-Druck notwendig bzw. von Vorteil ist.
Oft wird die Frage gestellt, ob der 3D-Druck von Ersatzteilen auch auf See denkbar sei. Die Reederei Maersk hat bereits im Jahr 2014 den Nachweis erbracht, dass die additive Herstellung von Kunststoffteilen mit dem FDM-Verfahren (engl. Fused Deposition Modeling) an Bord eines Schiffes möglich ist. Der Einsatz pulverbasierter Verfahren, wie sie für Metalle gebräuchlich sind, erscheint im Gegensatz dazu jedoch problematisch und kaum realistisch, da Seegang und Vibrationen das Aufbringen ebener Pulverschichten ausschließen und technische Maßnahmen zur Kompensation dieser Schiffsbewegungen in der Regel vermutlich zu aufwändig wären.
Stattdessen empfehlen sich »3D-Druck-Hubs« in ausgewählten, besonders stark frequentierten Häfen. In der Vision wird dorthin lediglich ein Datensatz verschickt, und kompetente Dienstleister übernehmen bedarfsnah die dezentrale Produktion von Ersatzteilen mittels verschiedener 3D-Druckverfahren, sofern die benötigten Bauteile für die additive Fertigung geeignet sind. Die Hafenbetreiber in Rotterdam und auch in Hamburg haben die Zeichen der Zeit erkannt und verfolgen aufmerksam die Entwicklung der additiven Fertigungstechnologien. Entscheidend für den Erfolg ist es dabei, das nötige Know-how aufzubauen, um wirtschaftliche Use-Cases zu erkennen, die dann als Referenz und Vorbild für weitere maritime Anwendungsfälle dienen.
Autor: Olaf Steinmeier, Fraunhofer-Einrichtung für Additive Produktionstechnologien IAPT
Eine Technik im Entwicklungsstadium
Das Unternehmen Rolf Lenk Werkzeug- und Maschinenbau sieht in der 3D-Drucktechnik großes Potenzial für die maritime Branche. Noch gilt es aber einige Hürden zu nehmen, vor allem bei der Zertifizierung.
Ein Unternehmen, das auf 3D-Druck setzt, ist Rolf Lenk Werkzeug- und Maschinenbau aus Ahrensburg, nordöstlich von Hamburg. Die Firma ist seit 1949 am Markt und hat neben dem Werkzeug- und Maschinenbau die additive Fertigung als wesentliches Standbein. Sie basiert auf der SLM-Technik (Selective Laser Melting), auch als 3D-Druck von Metallen bezeichnet. Das zu fertigende Teil wird schichtweise auf einer Substratplatte innerhalb eines Bauraums aufgebaut. Jede aufgetragene Schicht ist zwischen 30 und 600µm dünn und besteht aus metallischem Pulvermaterial. Mit Hilfe eines Lasers und der zuvor in einer Software erzeugten Schichten wird das Pulver aufgeschmolzen. Die Substratplatte senkt sich um die Höhe der Schichtdicke und der Vorgang wird wiederholt. Das Unternehmen besitzt zwei SLM 280 Twin mit einem Doppellaser und außerdem zwei Systeme vom Typ SLM 500 Quad. Diese verfügen sogar über vier Laser.
Seit sechs Jahren ist Rolf Lenk im 3D-Metalldruck tätig, anfangs kam hier ausschließlich das Pulverbettverfahren zum Einsatz, seit gut einem Jahr wird auch das 3DMP-Verfahren praktiziert. Nach Angaben des Geschäftsführenden Gesellschafters Gregor Sodeikat ist sein Unternehmen einer von wenigen Lohnfertigern in Deutschland, der über eine Maschine verfügt, mit der im 3DMP-Verfahren Teile hergestellt werden können. »Beim 3D-MP-Verfahren können wir annähernd jeden Schweißdraht bearbeiten, den es käuflich zu erwerben gibt«, sagt Sodeikat. Beim Pulverbettverfahren kämen die Pulver zum Einsatz, die auf dem Markt angeboten würden. Im Pulverbettbereich können komplexe Konturen hergestellt werden. Hier können auch teure Werkstoffe gefertigt werden, denn der Kunde bezahlt nur das, was verschmolzen wird. Prototypen oder Kleinstserien lassen sich mit diesem Verfahren ebenfalls produzieren.
Beim 3DMP-Verfahren könnten dagegen vorrangig großvolumige dreidimensionale Bauteile hergestellt werden, berichtet Sodeikat. Diese Technik funktioniert wie eine 5-Achsen-Fräsmaschine. Wo die Frässpindel ist, befindet sich die Schweißpistole. Im Prinzip wird hier nur der Draht geschweißt. Einfach bedienbar, digital gesteuert und automatisiert entsteht durch den Aufbau von Metallschichten ein Rohling, welcher im Anschluss mit Hilfe der mechanischen Nachbearbeitung seine Endgeometrie erhält. »Schon im Vorfeld sollte man sich Gedanken machen, wie diese Teile zu bearbeiten sind«, betont Matthias Otte, Projektleiter additive Fertigung bei Rolf Lenk. Materialien wie Edelstahl können verwendet werden, auch für größere Bauteile. Im Gussbereich sei dies ungünstig, da hier häufig Lunkerbildung auftrete, beschreibt Sodeikat.
Vergleich zweier 3D-Druckverfahren
Um beide 3D-Drucktechniken miteinander vergleichen zu können, hat das Unternehmen als Prototyp ein Blatt eines Verstellpropellers mit beiden Methoden hergestellt. Im Pulverbettverfahren habe die reine Druckzeit rund 70 Stunden betragen, im 3DMP-Verfahren seien es etwa 15 Stunden gewesen, berichtet Sodeikat. Entsprechend sei dieses Verfahren in diesem Fall wesentlich kostengünstiger. Dies hänge vor allem mit dem teuren Werkstoff Stahl zusammen, der bei der Nachbearbeitung sehr »zäh« sei. Somit sei der Werkzeugverschleiß beim Pulverbettverfahren sehr hoch, zudem würden viel Spähne erzeugt werden, ergänzt Otte. »Für den Kunden ist es daher sinnvoll, nur das aufzuschweißen, was aufgeschweißt werden muss«, sagt er. Das fertige Bauteil habe ein hohes Zerspahnvolumen.
Im maritimen Bereich lassen sich laut Sodeikat vor allem kleinere Propeller, insbesondere Verstellpropeller, mit der 3D-Druckttechnik fertigen, die beispielsweise auf Behördenfahrzeugen installiert sind. Die 3DMP-Maschine sei aber auch in der Lage, Propeller im Fünfachs-Bereich mit Durchmessern von 900 mm und Höhen bis 1.100 mm herzustellen, wie sie auf Frachtern zum Einsatz kommen. Im Dreiachs-Bereich sind es 1.100 x 1.400 x 1.560 mm.
Mit den 3D-Druckverfahren lassen sich also auch Propeller mit großen Durchmessern in geringen Stückzahlen herstellen. Im Gegensatz zum Gussverfahren wird hier keine Form benötigt. Ferner können mit der 3D-Drucktechnik Teile u.a. auch aus amagnetischem Stahl oder Titan gefertigt werden. »Im Allgemeinen lassen sich filigrane Teile eher mit dem Pulverbettverfahren fertigen, größere Teile mit größeren Wandstärken dagegen im 3DMP-Verfahren«, fasst Otte zusammen.
Zertifizierung bereitet Probleme
Derzeit setzt vor allem die Größe der Maschine die Grenzen für die Fertigung. Die Technik sei noch sehr jung, wo die Entwicklung in fünf oder sechs Jahren hingehe und welche Größe Maschinen dann hätten, könne man zum jetzigen Zeitpunkt nur schwer vorhersagen, sagt Sodeikat.
Aufträge aus der maritimen Branche sind derzeit eher die Ausnahme, berichtet der Unternehmenschef. Die Reeder seien noch vorsichtig. Sodeikat nennt Probleme mit der Zertifizierung dieser Technik als Hauptgrund für die abwartende Haltung der Branchenakteure. »Derzeit kann uns keiner sagen, welche Vorschrift hier gilt.« Bei den Klassifikationsgesellschaften gebe es durchaus Interesse, die 3D-Drucktechnik zu zertifizieren. Sie wüssten allerdings selbst nicht, nach welchen Vorschriften zu zertifizieren sei.
»Deshalb versuchen wir zunächst eine normale Schweißerzertifizierung zu bekommen, um eine Grundlage zu haben«, erläutert Sodeikat. In einem nächsten Schritt will er mit den Zertifizierungsgesellschaften sprechen, um die Zulassung für die Bauteile zu bekommen. Schließlich sei alles, was für den Antrieb eines Schiffes wichtig sei, abnahmepflichtig. Eine Zeitschiene konnte Sodeikat nicht nennen. »Uns bleibt derzeit nicht viel anderes übrig als zu warten.« Mit dem Kunden müsse daher in enger Zusammenarbeit mit der Zertifizierungsgesellschaft das jeweilige Projekt genauestens besprochen werden, um Sondergenehmigungen zu bekommen.
»Wir haben aber bereits für Kunden, die nicht aus dem maritimen Bereich kommen, Teile im 3D-Druckverfahren gefertigt, die sich auch in der Praxis bewährt haben«, sagt der Manager. Für die Deutsche Bahn habe man Ersatzteile für den ICE hergestellt. Es habe sich dabei um sicherheitsrelevante Bauteile gehandelt. Die Prüfung sei nach der Schweißnorm ISO 5817 von der SLV Nord durchgeführt und in die höchste Bewertungsgruppe B eingeordnet worden. »Die Teile werden in Zügen eingesetzt und sollen in naher Zukunft fahren. Es funktioniert also«, sagt Sodeikat.
Einige Vertreter von Werften haben Rolf Lenk bereits besucht und sich das 3D-Druckverfahren umfangreich erläutern lassen. Es habe positive Reaktionen gegeben, berichtet der 3D-Druckexperte. »Der finale Schritt fehlt aber noch.« Bis ein Bauteil eine Serienfertigung erlangt, dauere es daher wohl noch eine gewisse Zeit. Bekannt sei die Technologie zwar, derzeit überwiege aber noch die Skepsis bei den potenziellen Kunden, sie auszuprobieren.
Rolf Lenk ist Mitglied im Maritimen Cluster Norddeutschland (MCN) und nutzt dieses, um die 3D-Drucktechnik bekannter zu machen. »Wir müssen aber aktiv darauf aufmerksam machen, dass wir hier in Ahrensburg über Maschinen verfügen, die Teile im 3D-Druckverfahren für die maritime Branche herstellen können. Ansonsten passiert da nichts«, meint Sodeikat. Die Vorteile dieser Technik seien unbestritten, Herstellungskosten könnten gegenüber der konventionellen Fertigung je nach Bauteil um bis zu 60% reduziert werden. (twg)
16 Partner für 3D: Industrie-Projekt entwickelt Richtlinie
Das Potenzial von 3D-Druck ist auch in der maritimen Industrie groß. Weil der regulative Rahmen noch fehlt, arbeitet eine Gruppe von Unternehmen an einer Richtlinie.
Zu den Herausforderungen der Unternehmen in der maritimen Industrie gehören unter anderem Korrosion, lange Betriebsintervalle und die Alterung von Ersatzteilen. Innovative Fertigungsmöglichkeiten sind deswegen in der maritimen Industrie dringend notwendig. Eine potenzielle Lösung für diese Herausforderungen stellt die Selective Laser Melting Technologie dar. Im Bauraum der Maschinen des börsennotierten deutsche Unternehmens SLM Solutions mit Hauptsitz in Lübeck sowie einigen internationalen Niederlassungen wird Metallpulver mit Hilfe von mehreren, gleichzeitig arbeitenden Lasern Schicht für Schicht verschmolzen. So sollen in wenigen Tagen qualitativ hochwertige Bauteile entstehen können, die je nach Anforderung und Material sowohl korrosions- als auch hitzebeständig sind. Weil die Herstellung auch an »entlegenen Orten« direkt möglich sowie, je nach Anwendung, in einem kurzen Zeitraum realisierbar ist, kann die Bauteil-Logistik im Idealfall vereinfacht werden.
Die Anwendung von 3D-gedruckten Bauteilen ist allerdings, im Gegensatz zu anderen Industrien, in der maritimen Industrie noch selten, da keine standardisierten Richtlinien und Prozesse bestehen.
Um das zu ändern und die additive Fertigung für die maritime Industrie zu qualifizieren, haben sich zahlreiche Unternehmen zusammengeschlossen. Innerhalb von zwei aufeinander abgestimmten »Joint Innovation Projects« (JiPs) erarbeiten die mittlerweile 16 Partner eine Richtlinie sowie einen wirtschaftlichen Business-Case für die additive Fertigung, um so qualifizierte, funktionale Metallbauteile (Ersatzteile) für die Öl-, Gas- und maritime Industrie zu entwickeln. Zu den Partnern gehören: Equinor, BP, Total, Kongsberg, OCAS, Ivaldi Group, TechnipFMC, Siemens, Voestalpine, Vallourec, Aidro, SLM Solutions, Additive Industries, Quintus, HIPtec und das Advanced Forming Research Centre der University of Strathclyde.
Die Richtlinie soll dem Endverbraucher die Möglichkeit geben, sich auf die Erfahrung aller Partner in diesem Bereich und auf DNV GL-Vorgaben zu stützen, um so qualitativ hochwertige Bauteile für die jeweilige Anwendung zu beschaffen und/oder herzustellen. Insgesamt soll so nicht zuletzt die Kundenakzeptanz für die Technologie insgesamt erhöht werden.
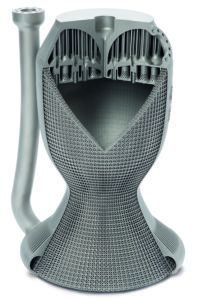
Wie die SLM-Technologie bereits erfolgreich in anderen Branchen eingesetzt werden kann, zeigt das Unternehmen CellCore GmbH, das in Zusammenarbeit mit SLM Solutions ein monolithisches Raketentriebwerk herstellte.
Das Bauteil – Injektor und Schubkammer – vereint integrales Design, also die Zusammenfassung der zahlreichen Einzelkomponenten in einem Bauteil, mit multifunktionalem Leichtbau. Kernelement ist die den Angaben zufolge nur mit Hilfe der SLM-Technologie zu fertigende, innenliegende, von CellCore entwickelte Struktur. Sie soll Stabilität garantieren und ist für den Wärmetransport geeignet. Die Eigenschaften dieser Strukturkühlung übertreffen konventionelle Ansätze, wie zum Beispiel rechteckige, konzentrisch verlaufende Kühlkanäle, deutlich.
Die Strukturkühlung biete ein optimales Verhältnis zwischen Stabilität und Masseneinsatz und weist einen geringen Strömungswiderstand mit gleichzeitig hoher Wirkungsoberfläche auf, heißt es. Sie sei somit nicht nur effizienter, es würden auch zusätzliche Funktionen integriert. Die Gitterstruktur sorge zudem für eine Gewichtsreduktion im Vergleich zu herkömmlich gefertigten Bauteilen.
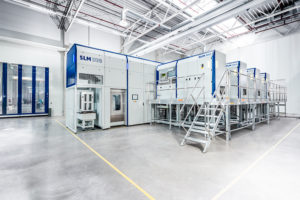
Sowohl in der Luft- und Raumfahrt als auch in der maritimen Industrie stellt die Bauteilgröße eine Herausforderung dar. Die Maschine SLM800 von SLM Solutions ist mit einem Bauraum von 500 x 280 x 850mm und einer Quad-Laser Konfiguration (4x 400W oder 4x 700W) auf genau solche Anwendungsfälle ausgelegt. Sie bietet mit einer Aufbaurate von bis zu 171cm3/h einem großen Bauraum sowie einem integrierten Pulverhandling neue Möglichkeiten in der Serienfertigung großer Bauteile.
Live-Simulation macht es möglich
In vielen Bauteilen, die uns im Alltag umgeben, schlummert ungenutztes Potential. So sieht es das Ingenieurbüro SMILE-FEM GmbH aus Heikendorf, dass sich deshalb der Aufgabe verschrieben hat, dieses Potenzial zu erkennen und zu nutzen.
Durch ein Umdenken weg von konventioneller und hin zu additiver Fertigung sollen sich Freiheiten im Design ergeben, die zuvor undenkbar waren. Mithilfe der modernen Simulationssoftware ANSYS Discovery Live und der Unterstützung von CADFEM konnte SMILE-FEM zeigen, welches Potential in einem Hydraulik-Steuerblock steckt. Durch Simulation und additive Fertigung konnten der Druckverlust um bis zu 50%, das Gewicht um 75% und die Bauhöhe um 28% reduziert werden.
Seit über zehn Jahren unterstützen die Berechnungsingenieure von SMILE-FEM Werften und Zulieferunternehmen, indem sie ausgereifte Konstruktionsentwürfe unter realen Bedingungen simulieren. Ziel ist es, das vollständige Potential der technischen Anwendungen nutzen zu können und erforderliche Nachweise für Klassifikationsgesellschaften zu erbringen. Neue Verfahren wie die additive Fertigung erlauben es, bisher bestehende Grenzen zu überschreiten.
Die technischen Herausforderungen bei einem solchen Projekt lassen sich nach Ansicht der Experten in zwei Bereiche unterteilen. Zum einen geht es um Gewichts- und damit um Materialeinsparungen. Zum anderen soll die Funktionalität des Bauteils verbessert werden. Diese beiden Aspekte müssen jeweils gemeinsam betrachtet werden, wenn ein wirklich gutes und erfolgreiches Produkt entstehen soll.
Dieser grundsätzliche Ansatz wurde an einem Bauteil erprobt, das in großer Anzahl auf modernen Schiffen zu finden ist. In jedem hydraulischen Aggregat, sei es eine Winde, ein Kran oder eine Komponente des Antriebs, werden zur Steuerung Hydraulik-Steuerblöcke eingesetzt. Diese sind bereits mit konventionellen Methoden sehr weit optimiert.
Anhand eines Prototyps wird dargestellt, welches Potential in der additiven Fertigung steckt. So wurde hier nicht nur eine erhebliche Gewichtsreduzierung angestrebt, sondern auch die Druckverluste in dem Hydraulik-Steuerblock sollten minimiert, Bauraum gespart und zwei Komponenten vereint werden.
Dies ließ sich nur dadurch erreichen, dass die bisherigen Einschränkungen durch die Fertigungsmethodik aufgehoben werden konnten. Denn bisher wurden die erforderlichen Kanäle in einen Rohblock gebohrt oder gefräst. Somit waren nur gerade Verbindungen mit konstantem oder sich verjüngendem Querschnitt möglich. Die additive Fertigung erlaubt dagegen auch gekrümmte Verbindungen, Verzweigungen und Hinterschneidungen.
In einem ersten Schritt wurden Anschlüsse neu arrangiert, um sie funktional aber auch platzsparend zu bündeln. Anschließend wurden die Kanäle neu gezogen. Dabei wurden sie so geformt, dass sie strömungstechnisch optimiert wurden. Es wurden tote Enden sowie scharfe Umlenkungen vermieden und möglichst kurze Verbindungen gewählt. Zudem wurden Verzweigungen strömungsgünstig ausgelegt. Mit diesen optimierten Kanälen als Negativmodell konnte die Geometrie der eigentlichen Struktur mittels Topologieoptimierung erstellt werden. Die optimierte Geometrie weist nun einen um 50% reduzierten Druckverlust, ein um 75% reduziertes Gewicht und einen um 28% reduzierten Bauraum auf. So werden nicht nur die Effizienz des Aggregats gesteigert, Gewicht und Material eingespart, sondern auch die Montage und die Wartung vor Ort erleichtert.
Auch wenn additive Fertigung derzeit in der individuellen Anwendung noch aus finanziellen oder fertigungstechnischen Gründen ausscheidet, so bietet ein frühzeitiger Einsatz von schnellen und effizienten Simulationstools das Potenzial, bereits während der Konzeptphase strukturelle Entscheidungen zu treffen. So kann bereits frühzeitig ein Weg in Richtung einer optimalen Funktion sowie eines effizienten Einsatzes der Ressourcen eingeschlagen werden. »Jede technische Anwendung ist individuell und benötigt individuelle Lösungen. In Zeiten immer fortschreitender Globalisierung und Digitalisierung ist es auch in der maritimen Branche essenziell, alte Denkmuster zu hinterfragen und ungenutztes Potenzial zu erschließen«, heißt es seitens SMILE-FEMs.
Schiffspropeller made with 3DMP
Wie sich der 3D-Druck als neue Fertigungsmethode auch im Schiffbau einsetzen lässt, zeigt eine Kooperation des Propeller-Herstellers Schaffran mit Gefertec.
Die Auslegung eines Schiffspropellers ist komplex und muss in den meisten Fällen auf das jeweilige Schiff angepasst werden. Die Herstellung von Schiffspropellern ist deswegen in der Regel eine Unikat-Fertigung, die Schiffgröße, Rumpfform, Antriebsleistung und viele weitere Faktoren berücksichtigen muss. Das Standardverfahren zur Herstellung von Propellern ist der Guss mit anschließender Endbearbeitung. Als Werkstoff kommt dabei eine Nickel-Aluminium-Bronze zum Einsatz. Auf Basis der Planungen wird zunächst ein Modell des Propellers, das in der Regel aus Holz besteht, angefertigt. Mit diesem Modell wird dann in der Gießerei die Hohlform für den Guss hergestellt. Aufgrund der Unikatfertigung wird das Modell nach dem Herstellen der Hohlform nicht mehr benötigt und deswegen weggeworfen.
»Wir sind als Hersteller für Schiffspropeller sehr an alternativen Fertigungsverfahren, wie etwa dem 3D-Druck, interessiert«, betont Matthias Eckert, Prokurist bei Schaffran. Deswegen habe er auch sofort zugesagt, als die Gefertec GmbH mit dem Vorschlag einer Kooperation auf ihn zugekommen ist. Das zur B.I.G. gehörende Unternehmen hat das 3DMP-Verfahren zur Marktreife entwickelt.
Es basiert auf dem sogenannten Auftragsschweißen und verwendet als Ausgangsmaterial Draht, mittels dessen Schweißraupe für Schweißraupe ein Werkstück gedruckt wird. Ein großer Vorteil dieses innovativen Verfahrens ist die sehr hohe Aufbaurate, die in Abhängigkeit vom verwendeten Werkstoff bis zu 600cm3 pro Stunde beträgt. Dadurch eignet es sich für die schnelle und wirtschaftliche Fertigung auch größerer Werkstücke aus Stahl, Nickelbasis, Bronze, Titan oder Aluminium. Im Rahmen der Kooperation hat Gefertec als Demonstrator den Flügel für einen Verstellpropeller mit dem Verfahren hergestellt.
Das Unternehmen verwendet das für einige Beobachter zum »inzwischen neuen Industriestandard avancierte« 3DMP-Verfahren in seinen Maschinen der arc-Serie. Diese sind in verschiedenen Modellen lieferbar: als 3-achsige Variante für Werkstückgrößen bis etwa 3m3, als 5-achsige Version für Werkstückgrößen bis 0,8m3 sowie als kompaktere 5-Achs-Variante für Werkstückgrößen bis zu 0,06m3. Eine speziell entwickelte CAM-Software erzeugt aus den CAD-Daten des Werkstücks die Daten, mit denen die CNC-Steuerung die exakte Positionierung des Schweißkopfs vornimmt. Die Fertigung des endkonturnahen Werkstücks erledigt die Maschine dann vollautomatisch.
»Da das 3DMP-Verfahren direkt mit den CAD-Daten arbeitet, kann das aufwändige Herstellen des Modells, wie es bei der Produktion im Guss-Verfahren notwendig ist, entfallen«, erläutert Eckert. Die Maschinen von Gefertec ermöglichen Unternehmensangaben zufolge eine »kostengünstige und schnelle Herstellung von endkonturnahen Rohlingen aus Metall«. Die Endbearbeitung erfolgt mit herkömmlichen Bearbeitungsverfahren, beispielsweise per CNC-Fräse. »Dies würde sich kaum von der Bearbeitung der Rohlinge unterscheiden, die wir aus der Gießerei erhalten«, sagt Eckert: »Die Qualität könnte sogar besser sein, da sogenannte Lunker – also Fehlstellen im Rohling –, die beim Gießen stets auftreten können, beim 3DMP-Verfahren ausgeschlossen sind.«
Der Hauptvorteil des 3D-Drucks mit dem 3DMP-Verfahren ist nach Meinung des Schaffran-Prokuristen die Geschwindigkeit: »Dies könnte einen deutlichen Zeitgewinn ausmachen – dazu trägt natürlich auch bei, dass wir kein Modell mehr fertigen müssten.« Eine Hürde ist allerdings noch zu nehmen, bevor das Verfahren für die Fertigung von Propellern verwendet werden kann, wie Eckert weiß: »Die Prüfung und Zertifizierung des 3DMP-Verfahrens durch eine Schiffsklassifikationsgesellschaft steht noch aus.« Auch ist der maximale Bauraum der arc-Maschinen bisher noch nicht für sehr große Schiffspropeller geeignet.
DNV GL treibt 3D-Druck voran
Die additive Fertigung steht auch bei der Klassifikationsgesellschaft DNV GL auf der Agenda. Zuletzt gab es in diesem Jahr einige nicht unerhebliche Entwicklungen, etwa im Marine-Schiffbau.
So wurde beisielsweise eine Herstellerzulassung an das thyssenkrupp TechCenter Additive Manufacturing ausgegeben. Der Konzern arbeitet eng mit internationalen Kunden an der Integration von additiv gefertigten Bauteilen auf Schiffen und in U-Booten zusammen und hat deshalb einen Bedarf an Bauteilen mit Abnahmeprüfzeugnis. Derartige Verfahren und Prozesse seien weltweit bislang nicht verfügbar gewesen und sind deshalb in enger Zusammenarbeit entwickelt worden, nun habe man als weltweit erster Produzent von 3D-Druck-Bauteilen für den maritimen Bereich eine Herstellerzulassung von DNV GL erhalten, bestätigte thyssenkrupp jüngst.
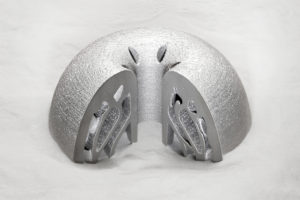
»Additive Fertigung wird in Zukunft einen erheblichen Einfluss auf die maritime Produktionskette nehmen. Von zentraler Bedeutung ist hierbei, dass diese Komponenten genauso hochwertig sind wie konventionell gefertigte Produkte und dass sie die Anforderungen an die Klassifikation erfüllen. Uns freut sehr, dass das thyssenkrupp TechCenter Additive Manufacturing die zuverlässige Produktion von metallischen Werkstoffen mittels Additiver Fertigung erfolgreich unter Beweis gestellt hat. Damit wird es zum ersten Unternehmen weltweit, das von DNV GL mit dem sogenannten Zertifikat »Approval of Manufacturer for Additive Manufactured Metallic Materials« ausgezeichnet wurde. Herzlichen Glückwunsch zu dieser außerordentlichen Leistung«, sagte Geir Dugstad, Direktor für Schiffsklassifizierung und Technischer Direktor bei DNV GL – Maritime.
»Wir sind sehr erfreut darüber, jetzt einen zertifizierten Partner an der Seite zu haben, der thyssenkrupp Marine Systems mit additiv gefertigten Teilen versorgen kann, die sowohl unsere als auch die hohen Anforderungen unserer Kunden erfüllen. Gemeinsam bringen wir innovative Lösungen auf unsere U-Boote und Schiffe und schaffen so den Standard der Marine von morgen«, so Luis Alejandro Orellano, Chief Operating Officer der thyssenkrupp Marine Systems. Das Zertifikat bedeute, dass das thyssenkrupp TechCenter Additive Manufacturing als Lieferant für maritime und allgemeine industrielle Anwendungen zugelassen ist.
Die Herstellerzulassung beinhaltet den 3D-Druck von Teilen aus austenitischem Edelstahl sowie deren Nachbearbeitung. Zertifiziert sind auch der Abnahmeprozess gemäß EN 10204 und die dazugehörigen Produktinformationen, insbesondere die chemischen und physikalischen Materialkennwerte. Außerdem sind den Angaben zufolge Zulassungen einzelner, spezieller Komponenten in Vorbereitung.
DNV GL-Experten aus mehreren Einheiten koordinierten, um zu prüfen, ob die Prozesse des TechCenters zuverlässig sind und eine gleichbleibende Qualität gewährleisten. »Eine Teamarbeit war hier besonders wichtig, denn die Zertifizierung erforderte ein Überdenken der traditionellen Methoden zur Qualitätsbewertung und -zertifizierung. Ich möchte allen Beteiligten für ihre Unterstützung und Zusammenarbeit danken«, sagte Eva Junghans, Senior Principal Engineer, Materials & Welding bei DNV GL – Maritime.
Zuvor war im Frühjahr bekannt geworden, dass die norwegisch-deutsche Klassifikationsgesellschaft als leitende Forschungsstelle an der ersten Phase eines neuen, in Singapur gestarteten Programms teilnimmt. Es hat zum Ziel, die Machbarkeit von Additiv Manufacturing (AM) oder 3D-Druck in der maritimen Industrie zu untersuchen. In einem von der Maritime and Port Authority of Singapore (MPA) initiierten gemeinsamen Industrieprogramm (JIP) untersucht DNV GL gemeinsam mit zehn Mitgliedsunternehmen der Singapore Ship Association (SSA), wie von 3D-Druckern produzierte Ersatzteile der kapitalintensiven Industrie helfen können, Kosten und Ausfallzeiten zu senken. Die Ergebnisse sollen mehr maritime Akteure ermutigen, AM zur Optimierung ihrer Ersatzteilversorgung einzusetzen und nicht zuletzt den Status Singapurs als One-Stop-Shop mit Hafendienstleistungen zur Unterstützung eines vielfältigen Betriebs von Reedereien und Schifffahrtsunternehmen stärken.
Im Jahr 2018 hatte DNV GL bereits den ersten »Approval of Manufacturer«-Plan veröffentlicht – gerichtet an Hersteller, die additiv gefertigte Produkte gemäß den Normen der Klasse fertigen wollen. 2017 war der erste Leitfaden für den Einsatz von 3D-Druck in der Schifffahrts-, Öl- und Gasindustrie veröffentlicht worden.
HANSA International Maritime Journal | Report 3D-Druck & Additive Fertigung | Oktober 2019
Chefredakteur: Krischan Förster | Stellv. Chefredakteur: Michael Meyer | Redakteure: Felix Selzer, Thomas Wägener
Schiffahrts-Verlag »Hansa« GmbH & Co. KG | Stadthausbrücke 4 | 20355 Hamburg | redaktion@hansa-online.de | Tel +49 (0)40-70 70 80-02 | Fax -214