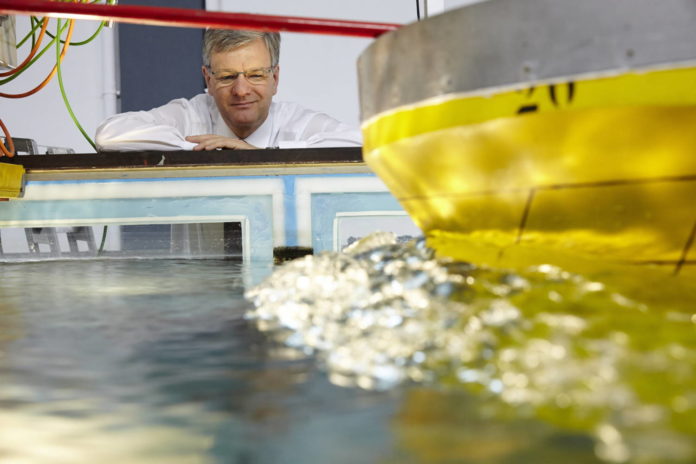
Voith Turbo is extremely busy in looking deeper into the hydrodynamic aspects of
the interaction between hull and propulsion unit. A special focus lies on tugs, which
are optimised regarding their operational window, DP capabilities, manoeuvrability,
and energy efficiency.
[ds_preview]Voith Turbo is situated in Heidenheim an der Brenz, a town in the southern part of Germany at a tiny river. Here, tugs will only be seen in model scale, since the coastline is approximately 700 km away. However, at the company premises the propulsion specialist has gathered a lot of know-how in the hydrodynamics of such vessels.
Tugboats face the demands of either low-speed assist operations or high-speed escort operations, which are quite contradictory. If both ways of performance need to be united in one tug, it is the task of ship designers to work out reasonable compromises. Dirk Jürgens, Head of the R&D department and Vice President of Voith Turbo, gives an overview about the research activities of the propulsion experts.
Research & Development is a big issue at Voith. Many companies are outsourcing these activities, while Voith continues to keep the R&D department in-house. What is the background of this decision?
Dirk Jürgens: Research and Development is essential for the design of our products. Our credo »engineered reliability« can only be fulfilled if we can guarantee the quality of all details of our propellers. For a reliable product design it is essential to know the loads and the stress levels of each individual part. This is only possible by applying modern R&D techniques such as numerical methods (e.g. CFD, FEM) and simulator tools.
It is our ambition to support our customers not only by delivering a reliable propulsion system, but by assisting them in designing an efficient vessel, which works safely even in very exposed conditions. This can only be achieved if we have efficient R&D resources consisting of the right people, methods and facilities. Although we have no intention to outsource our R&D activities, we have many external R&D partners to improve our products. These are mainly model basins and universities.
Being situated in an absolutely non-marine environment, only an excellent reputation can attract highly qualified engineers. What can you offer to them?
Jürgens: Our R&D department has various specialists. We have naval architects, mechanical engineers, electronic engineers, a mathematician, an IT engineer and measurement engineers. We are offering the design of new vessels including the prediction of speed, bollard pull, DP capabilities, reduction of roll motion and many other important details. To do this, we have our own model tank test, a ship manoeuvring simulator and powerful CFD capacities.
Do you understand yourself as a consultant for a shipowner who wants to have ›just‹ the propulsion solution for an efficient and high performing tug? Or are you also offering general design solutions for the whole vessel?
Jürgens: We are able to support the shipowner in all phases from the concept design to the sea trials and any later modifications of the vessel. We also offer our support to ship design offices and enjoy cooperating with them to find the best solution for the shipowner and his vessel. Our target is the design of an efficient and safe vessel concept with a very low total cost of ownership.
For more than 13 years you have been working with CFD. How close are you approaching reality – cross checking with traditional experimental methods?
Jürgens: We have indeed started quite early with the industrial usage of CFD in the year 2000. We trust in our CFD results because we ensure a very high quality of the finite volume mesh as the basis of the calculation and the precise solving of the governing equations. From as early as 2000, Milovan Peric from CD-adapco has been our reliable partner in this respect.
As an ongoing process we also carry out a permanent comparison of CFD results and measurements either in model or in full scale. Our participation in many national and international R&D projects also helps a lot. Model tests offer a very good tool for validation, but the scale effects increasingly prove to be an obstacle. Last year, we therefore started various activities to measure in full scale. It is costly but the right way to further improve our products.
Your department includes a training simulator, to give your clients the opportunity to learn how to manoeuvre a ship with a Voith Schneider Propeller (VSP). What is the main purpose of the simulator: external use or internal testing?
Jürgens: Our simulator is mainly used to answer important questions of our clients such as: What is the right tug size for my port, which power does my ferry need, can I keep the position of my platform support vessel dynamically in exposed condition, and many more.
Training is not our main focus for the simulator, but we are offering special courses like fuel-efficient ship assistance, safe escorting of tankers, precise dynamic positioning and others. Because of our deep insight into the hydrodynamic principle, our customers enjoy these special courses and very often they lead to new product ideas.
Furthermore, we use our simulator as a basis for partnerships with larger simulator training centers. We have developed and tested software elements, which accurately describe the hydrodynamics of our propulsors, especially the Voith Schneider Propeller, and the ship types that are relevant for our products. These software elements can easily be linked in by any other simulator centers. The fact that we have our own simulator has enabled us to develop and extensively test such software systems.
In 2011 you started a cooperation with Robert Allan, called »RAVE Tug«, which is a new concept of a high performance escort tug. How far have you proceeded with this project?
Jürgens: RAVE Tug, which stands for is a very interesting tug concept. It offers safe and efficient new ways for ship assistance. The development was initiated by Oscar Lisagor from Robert Allan, and we jointly carried out all the necessary development steps, such as conceptual design, ship line development, CFD and model testing as well as extensive simulator studies in cooperation with the captains of our potential customers. We are now working on very concrete projects and hope to build the first prototype soon. The first customer will play a key role, of course. Although there are many questions that have to be answered, Robert Allan and Voith together have the knowledge and the tools to successfully design a new revolutionary tug with RAVE.
High fuel costs also affect the offshore industries. In your research project »Comparative investigation on influence of the positioning time of azimuth thrusters on the accuracy of DP« you were not only looking on the mere engine performance and fuel consumption but also on the awareness of the crew. Could you give us an impression of this project?
Jürgens: The VSP offers a new quality of dynamic positioning. Accuracy and low fuel consumption are based on the fast and very accurate thrust allocation of the propeller. For the assessment of vessels regarding their DP capabilities, static DP plots are the current method. But in real life a fast response against disturbances caused by waves, wind and currents is essential. Therefore, we have started an R&D project together with the Technical University of Hamburg, the University of Rostock and the Potsdam Ship Model Basin, which will clearly show the importance of fast response against such disturbances.
A huge – and already finished – project was »SafeTug«. What did you find out there?
Jürgens: This R&D joint industrial project, which was led by the Maritime Research Institute Netherlands (MARIN), examined, among other factors, the limits of tug operations in exposed conditions. During the project it was discovered that the roll motion is the limiting factor for tug operations. We have developed and successfully launched the Voith Roll Stabilization where we can reduce the roll motion in a range from 30–90 % depending on the ship’s parameters. Since 2007, this system has been in practical operation on many VSP-driven vessels and works very reliably. From the SafeTug project we know that the Voith Roll Stabilization will enlarge the operational window of VSP tugs. The crew will benefit from this feature because it improves their working conditions.
What are other current topics you are looking at?
Jürgens: We have of course many new projects. Besides the RAVE development mentioned earlier we are working on new ship concepts. A very interesting example is the Voith Offshore Shuttle, which enables the safe transfer of service engineers to offshore wind turbines because of
the excellent manoeuvrability of the Voith Schneider Propeller.
Another exciting development is the Voith Linear Jet (VLJ), where we are in the process of testing the first prototype in full scale soon. The VLJ is a new business area for us where we are offering efficient propulsion for fast vessels.
One last example, which I would like to mention, is the successful development of our own electronic remote control system. The first system works reliably on a hybrid ferry in Scotland. There, the hybrid system is uniquely supported by the variable-pitch characteristic of the VSP and the new control system. The applied combinator curves were optimised by the usage of our CFD tools and by intensive simulator tests. The reduction of fuel consumption and emissions is remarkable.
Kerstin Klinkenberg