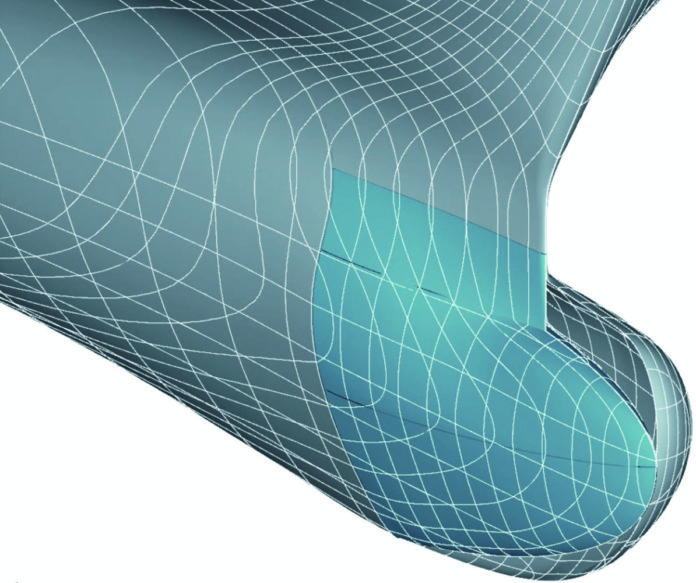
Formal optimisation can be applied to complete ship hulls, but also to selected portions of a hull. The latter case makes bulbous bow refits an attractive option, especially for container ships in times of slow steaming. A case study shows fuel savings of 6 % for
a large vessel, as Karsten Hoc[ds_preview]hkirch and Volker Bertram of FutureShip report
Fuel efficiency is bound to stay the dominant topic in shipping for years to come. It is well known that hull optimisation is one of the most important levers for fuel efficiency in newbuildings. However, re-design and refit of bulbous bows is often not considered at all for ships in service. This oversight is understandable as the achievable savings are frequently underestimated even by experts.
While naturally obtainable fuel savings are significantly larger for complete hull optimisations, optimisation of the bulbous bow region alone offers still potentially very attractive fuel efficiency gains, especially for high powered large container ships which now operate frequently in off-design conditions. State-of-the-art optimisation for a realistic operational profile rather than a single design point opens the door to significant further fuel savings, also for refits. This will be demonstrated for a recent project of hull optimisation technology leader FutureShip.
(Partial) ship hull optimisation: Employed tools
The results of any optimisation project depend on the software tools employed and on the skill and experience of the project engineers. Many so-called hull optimisation projects fall short of what the best in the field can achieve. The reasons are manifold:
• False labelling: Simple improvement e.g. guided by CFD (computational fluid dynamics) analysis is called »optimisation«.
• Choice of optimisation objective: Rather than yearly fuel consumption, a single design point is chosen; then perhaps only the resistance is minimised rather than the required power or instead of high-fidelity CFD code a simpler software is employed introducing errors in the hydrodynamic assessment of variants.
• Restricted form variation: The investigated form variations depend on the fundamental (parametric) model. Unfortunate set-up of the parametric model may then prevent finding superior designs.
FutureShip employs a range of state-of-the-art tools in its optimisation projects:
• Friendship Framework for parametric hull modelling
• FS-Flow – Fully nonlinear wave resistance code based on potential flow theory
• Fine/Marine as high-fidelity viscous CFD code
• FS-Equilibrium for hydrostatic analyses (as required for constraints in ship stability)
• FS-Optimiser – toolkit for design space exploration and optimisation offering a variety of optimisation algorithms
Case study: Bow refit for a 13,000 TEU container ship
The shipowner realised the opportunities of a bulbous bow refit for his fleet of 13,000 TEU ships. The task was now to find the best solution for the fleet. Qualitatively, the larger the cut-out is chosen, the higher are the costs for the refit, but also the potential gains. In this particular case, there were two general options for such a refit:
• Option 1: Larger cut-out covering the ship below the waterline and before the collision bulkhead.
• Option 2: Smaller cut-out below the waterline and before the forward perpendicular.
The shipowner supplied records of actual operational data for the ship for a whole year. This database of speeds and drafts was condensed to eight representative clusters of speed-draft combinations with associated weights ranging between 10 and 25 %. The objective was then to reduce the combined fuel consumptions for these eight operational states, considering their time share in yearly operation.
A parametric model was set up for the bow section, employing 26 free parameters. The high number of parameters ensured that a vast number of possible bow shapes could be created. In any case, a harmonious fit with the rest of the hull was ensured by suitable constraints on the hull-bow intersection. Roughly 20,000 bow variants were investigated. Two final hull shapes were identified featuring optimal performance measures across the operational profile. As expected, the larger flexibility of Option 1 resulted also in larger possible fuel savings. Option 1 had expected gains in off-design conditions of up to 11 %, yielding expected yearly fuel savings of ~3.5 % for the actual operational profile. Option 2 had expected gains in off-design conditions of up to 6 %, yielding expected yearly fuel savings of ~1.8 % for the actual operational profile. Results were validated by »numerical sea trials« (high-fidelity CFD simulations for full-scale ship) and model tests.
Depending on size of fleet, employed repair yard and assumed fuel oil price, there are some variations in payback times, but all realistic scenarios show payback times between two and eight months, making this refit a good business decision by anybody’s standards.
Authors:
Dr. Ing. habil. Volker Bertram
Dr. Karsten Hochkirch
both at FutureShip GmbH, Hamburg,
Germany, www.futureship.de
Karsten Hochkirch, Volker Bertram