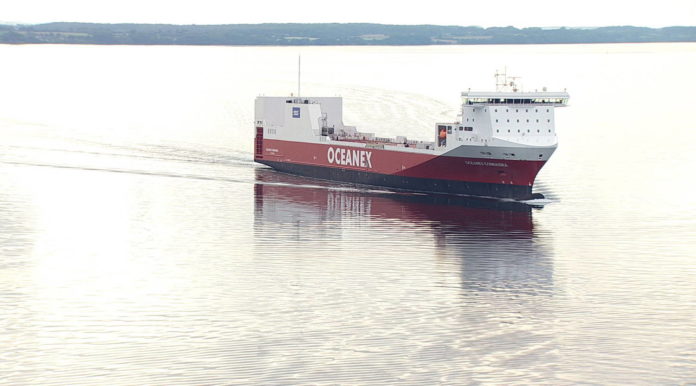
On 27 October 2013 Flensburger shipyard delivered one of the most modern, eco-friendly LoRo vessels afloat with outstanding fuel economy
Hull no. 757, named »Oceanex Connaigra«, is the first ship in the world to boast a dry exhaust gas cleaning system and thus meets regulations in all Em[ds_preview]ission Control Areas (ECAs). Flensburger shipyard won this order from the Canadian transport company Oceanex Inc. based in St. John’s, Newfoundland and Montreal. Oceanex provides intermodal transportation services throughout eastern Canada and carries about 80% of all freight to Newfoundland.
The new LoRo vessel (Lift on/off, Roll on/off), which is ice-classed DNV 1A, is designed for worldwide operation and will mainly be operated in the harsh conditions of the sea area on the east coast of Canada. Future environmental stipulations were also taken into consideration. For example, the later installation of a ballast water treatment plant has been catered for by providing the required space and equipment connections.
The 19,300 dwt newbuilding is 210m long, 29.6m wide and has a scantling draught of 8.6m. »Oceanex Connaigra« is highly flexible in operation and capable of carrying a broad mix of cargo types.
Design process
The bespoke design of the vessel has been developed by Flensburger Schiffbau-Gesellschaft (FSG) in close cooperation with the shipowner, thus making sure that all of Oceanex’ comprehensive requirements were properly taken care of to suit not only the present but also future market requirements. In order to closely follow the design process Oceanex was provided a software which enabled them to navigate in the FSG 3D CAD model from their offices in Canada. The data was updated every night, thus providing the latest view on the vessel.
This taylor-made design is defined by a complex matrix of requirements and influencing factors which had to be incorporated simultaneously, including a large range of drafts on different routes with very different kinds of cargo and loading operations in different ports under tidal conditions, operation in ice, highest fuel efficiency and heavy weather capabilities. Changing a certain design parameter usually affects a number of others which have to be checked always in parallel with respect to the formulated design goals. This generates a huge demand for calculations and simulations. In order to achieve the optimum design for the desired service, extensive calculation and simulation studies were carried out by the shipyard’s design team. By keeping all expertise in-house, FSG is able to offer a very flexible and fast product development process higly focused on the individual requirements of the customer.
Cargo
The vessel combines RoRo decks for cars and trailers with a weather deck suitable to stack 11,000t of containerised cargo in four tiers. Designed for adaptability to the conditions in the different ports of call, cargo access into the vessel is provided by a 12m wide stern ramp as well as by a 6m wide side ramp. To enable fast loading and unloading, the ship has an internal ramp system to access the truck and car levels. A hoistable ramp is part of this, linking the main deck with the weather deck. The weather deck foundations as well as the vessel’s ramp configuration and clear deck heights allow for transport of a wide range of cargo such as containers, trucks, cars and project cargo for the construction industry. The new vessel is also able to carry dangerous goods of Classes 1–9 (except nuclear cargo as defined in Class 7). The total deck area of this flexible LoRo ship is ca. 13,700m2 and the most diverse types of cargo may be stored there. The ship provides 2,700 lane metres for trucks and trailers on eight lanes or 6,200 lane metres for cars. Below the main deck a separate, fixed 2.05m high deck for cars is designed which provides space for 208 vehicles. 159 cars can be accommodated on a liftable deck in the lower cargo hold. Trailers are primarily parked on the main deck and on the lower deck. The main deck boasts a height of 5m/6.2m and offers 520m2 for project load/oversized cargo. The lower cargo hold is 4.5m high (2.25m in way of the liftable car deck). The 1,800m2 liftable deck is installed in the lower cargo hold.
The weather deck is available for containerised cargo up to 11,000t. It can take all current container sizes and provides slots for an equivalent of 940 TEU. Since the weather deck is also accessible from the main deck via a hoistable ramp, it can be used as a RoRo deck with a total area of 4,200m².
Efficiency
The vessel’s design has been optimised thoroughly to provide the lowest possible fuel consumption. This included extensive CFD studies in order to achieve a low wave-making resistance as well as a homogenous wake field which is a prerequisite for achieving a high propulsive efficiency and an efficient propeller design. It is important to mention that these investigations were not only carried out for the contractual design conditions but focussed on the real expected operating profile of the vessel including a range of common service drafts as well as service speeds.
Applying a holistic design approach the hull form provides well- balanced characteristics, not solely focusing on fuel efficiency but also taking into account stability, seakeeping and manoeuvring aspects. The results of the CFD studies have been verified by resistance and self propulsion model tests carried out at Force Technology in Denmark.
Propulsion plant
The ship’s main propulsion system consists of two 8,400 kW MAN main engines type 7L48/60CR. They operate via a reduction gearbox onto a controllable pitch propeller plant which also allows for single engine operation. The declutched main engine can be utilised in PTO mode to generate electrical power. The energy acquired in this way can be utilised, among other things, to provide power needed for 120 reefer containers and 300 heated containers.
The automation allows for operation in constant revolutions mode as well as combinatory mode. The vessel features a special estuary mode for operation on the Saint Lawrence River at slow speed where propeller revolutions are reduced in order to avoid the risk of face side cavitation at reduced pitch.The combinatory curves, determining the combination of engine revolutions and propeller pitch setting, were optimised for fuel efficiency, leading to up to 500 kW less power demand compared to standard curves.The combination of the propeller with the high-lift twist flow rudder specifically adapted to the propeller slip stream, equipped with an optimised Costa bulb design, allows for a high overall propulsive efficiency by partly regaining rotational losses.
While operating at moderate 98 rpm in design conditions, the propeller combines high efficiency with very low pressure fluctuations, cavitating as well as non-cavitating components, which enables a very low level of propeller-induced noise and vibrations on board. The propeller performance was verified by cavitation tests at Hamburg Ship Model Basin’s HyKat.For harbour manoeuvring operations the ship has four transverse thrusters of total 5,600 kW. This permits manoeuvring without tug assistance and inside winds of up to force Bft 7. The size of thrusters was not only chosen on account of the general harsh weather conditions but also to ensure safe operation in the confined space at Bickerdike terminal in Montreal.The operation of the machinery complies with the requirements of the classification society for a period of 24 h unattended services.
Emission control
To reliably meet the strict requirements of MARPOL Annex VI as of 2015, with regard to sulphur emissions during heavy fuel oil ship operation, the ship is fitted out with a dry absorption exhaust gas cleaning system (DryEGCS). »Oceanex Connaigra« is the first ship in the world to commercially utilise this technology. The dry absorption process – a method used successfully and globally for decades in land-based power stations to reduce sulphur in exhaust gases – is now also used in shipping. Compared to a wet scrubber system the impact on the electrical balance is almost negligible.
Seakeeping
The ship operates in a harsh sea environment with significant wave heights of up to 12m related to a 25-year return period. Thus one of the central requirements towards the ship design was a safe and reliable operation even in very rough conditions.
Due to the heterogeneous cargo mix the optimisation of the seakeeping performance was not only focused on one design loading condition but on a wide range of draughts and loading conditions. The stability of this variety of loading conditions differs considerably, ranging from container stowage on the weather deck showing large draughts and low stability to transport of mainly cars at low draught and very high ship stability. The seakeeping behaviour in these diverse loading conditions has significantly different characteristics with vulnerability to different physical phenomena. FSG has carried out extensive seakeeping simulation studies, which include criteria addressing motion amplitudes, in particular roll motions as well as lateral and vertical accelerations. Based on the latter, cargo criteria were used to assess the risk of sliding of unlashed cars and trucks. In addition, the hull was tested against FSG’s internal dynamic stability standard ISEI (Insufficient Stability Event Index), addressing the risk of large amplitude rolling such as parametric rolling and pure loss of stability. The result is a hull form showing small lever arm alterations in waves which reduce the risk of parametrically excited roll motions. The slender forebody reduces slamming loads as well as vertical accelerations. Roll damping is provided by bilge keels fitted to both sides of the hull. In order to improve the vessel’s seakeeping characteristics over the full range of different loading conditions and related natural roll periods, the ship is equipped with three flume tanks. These are tuned individually by CFD calculations and model tests in close cooperation with the supplier to counteract the roll motion over the full range of relevant natural roll periods. To further improve roll reduction, the vessel is additionally equipped with fin stabilizers providing an additional redundancy related to roll damping. Due to the vessel’s passive and active stabilisation systems, FSG could demonstrate that lashing is only required during periods of extreme weather conditions. The economical implications were pointed out by Captain Sid Hynes, Executive Chairman of Oceanex Inc.: »We hope to have the most stable platform that is reasonably possible, which will enable us to reduce lashing costs over the life of the ship. It costs a lot of money and shipping time to lash and unlash every trip. We see having stabilizers and flume tanks as a way to reduce the lifecycle costs on the ship.«
Construction
The first steel was cut on 8 October 2012 and less than four months after keel laying in FSG’s covered building berth the »Oceanex Connaigra« was launched on 31 May 2013. Following successful sea trials the change of flag was carried out on 27 September – three days ahead of schedule.
Contact:
Thomas Ritte, Vice President Sales
Flensburger Schiffbau-Gesellschaft (FSG)
Batteriestraße 52
24939 Flensburg/Germany
Tel. +49 (0)461/4940-575
ritte@fsg-ship.de, www.fsg-ship.de
Thomas Ritte