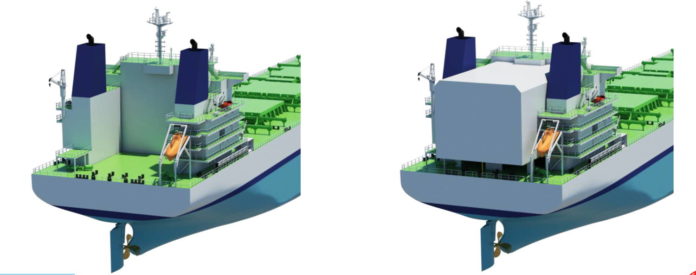
Norwegian-German classification society DNV GL has presented a number of projects[ds_preview] and initiatives during the exhibition. One example is an »Approval in Principle« (AiP) which was given Oshima Shipbuilding Company for a LNG-fuelled Kamsarmax bulk carrier. The new design has been found to comply with DNV GL class rules and all current and upcoming regulations, including the new emission control regulations and the draft IGF Code for fuel with a low flashpoint. As space on deck is limited on a bulk carrier, the design features an »innovative solution«, the partners said – changing the ship’s superstructure to a U-shape that can accommodate the LNG tank in its centre. Meanwhile, a tank cover adds an additional safety barrier and ensures compliance with the draft IGF Code. The bunkering stations for LNG, heavy fuel oil (HFO) and marine diesel oil are located at the side of the accommodation deck house. Oshima’s Manager Tatsurou Iwashita pointed out: »Our design does not reduce the vessel’s cargo capacity.« The vessel’s parameters are also based on data generated in a DNV GL feasibility study from 2014 that examined the use of LNG in a trade route between Europe and North America from a technological and economic perspective. DNV GL found that a LNG-fuelled Kamsarmax bulk carrier, which only uses LNG in Emission Control Areas, would require 500–700m3 of LNG and one bunkering operation for a round trip between Europe and North America. If it were powered with LNG for the entire voyage, it would require 2,000–2,500m3 of LNG.
Additionally, Hyundai Heavy Industries (HHI) was presented an AiP for the »SkyBench« concept for mega box ships. It is an design to increase cargo capacity. The bridge and upper three decks of a »twin island« design container would be constructed as a separate sliding block, mounted on rails and able to move over the length of two 40 ft container bays. In combination with a resizing and relocation of fuel tanks and the utilization of the void spaces beneath the accommodation block in a traditional design, this allows the addition of two extra 20 ft container bays. The mechanism takes ten minutes to operate. The two 40 ft side casings on which the accommodation block rests provide structural strength and hold lifeboats, provision cranes and utility rooms. In an emergency, the sliding block is detachable and is designed to float independently of the vessel.