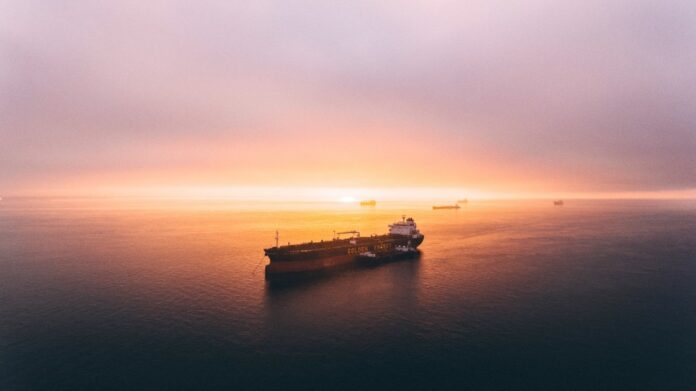
As shipping faces an era of new fuels and new engine designs to accommodate them, what role will cylinder lubrication play in enabling efficient and reliable engine operation? Lubricants supplier Chevron gathered what is known about the many unknowns yet[ds_preview]
The IMO sulphur cap already saw the emergence of very low sulphur fuel oil (VLSFO), the IMO long-range carbon target will encourage the introduction of even more new ship fuels. Alternatives like LNG and methanol are already in use and fuels such as ammonia, hydrogen and ethanol are being developed alongside lower-carbon synthetic and biomass-derived versions of conventional fuels. So-called e-fuels, which are produced using renewable energy, are also being developed.
Like VLSFO, each of the above fuels bring specific challenges to engine and cylinder condition that can be mitigated by careful handling, specific engine design and an appropriate lubrication regime, a whitepaper recently published by Chevron says.
At the same time, engine design will continue to advance — both to accommodate different fuels and to continue advancing efficiency. With new engine designs come new cylinder condition requirements. Higher cylinder pressures or temperatures require better performing lubricants, for example, and new combustion concepts may also demand different properties from lubricating oils.
History lessons
Previously engines had been optimised for high speeds and high engine loads. But a new era focused on fuel efficiency rather than maximal power output demanded different designs. The solution was found in longer piston strokes to enable slow engine speeds while turning bigger, more efficient propellers. Higher pressures and longer piston strokes exacerbated the issue of cold corrosion that caused ship operators to adapt their lubrication strategies to minimise the negative effect of sulphuric acid. The best way was to select a lubricant oil with an appropriate amount of alkaline material (indicated as base number or BN) to neutralise the sulphuric acid before it could cause damage. And another important lubricant practice was reinforced by the threat of cold corrosion: the need for regular analysis of used cylinder oil to identify warning signs.
The link between sulphur and BN, and the need for careful monitoring of drain oil, came to the fore once again as the industry prepared for the the IMO’s global sulphur cap, limiting the sulphur content in fuel to 0.50 %. This led to the introduction of an entirely new fuel type, very low sulphur fuel oil (VLSFO). The lower sulphur content of VLSFO meant a lower BN lubricant was needed. Simple enough, but the great fuel switch was not without issues. Being a blend, there is inherent variability in VLSFO depending on the constituent ingredients.
From cold corrosion to VLSFO, the recent past of cylinder condition highlights some useful insights as the maritime sector prepare for future fuels and engine design changes:
- There can be no one-size-fits-all approach to cylinder lubrication: High-sulphur fuels require different oils to low-sulphur fuels and the fuels shipping uses in the future are likely to raise further, different condition challenges requiring new formulations.
- Cylinder condition depends on the engine as much as fuel: Whether it is super-long stroke pistons exacerbating cold corrosion, or older engines struggling with the challenges of VLSFO, engine design and condition must be taken into account in cylinder lubrication.
- Any lubrication regime for new engine designs or new fuels will require vigilant monitoring for indicators of potentially problematic cylinder condition factors.
- Future fuels and cylinder condition
Perhaps the greatest unknown factor in managing cylinder condition in the future is which fuels will be preferred: Ammonia, methanol, LNG and synthetic (including biofuel) hydrocarbons? Each of these four future fuels has its own impact on cylinder condition. For synthetic hydrocarbons, the challenges would be similar to those accompanying use of current HSFO, marine diesel or whichever fuel is to be replicated. For LNG and methanol, there is already growing understanding of the required lubrication regime. Only ammonia remains unknown.
The first dual-fueled two-stroke ship engines were ordered in 2013. The general advice for two-stroke engines is: When the engines are operated on gas, the resulting fuel mix (gas and pilot fuel) is generally equivalent to an ultra-low sulphur fuel as the gas contains very little, if any, sulphur, and the amount of pilot fuel is small. When the engine switches over to liquid fuel operation, the engine acts like a diesel engine, and it may be subject to cold corrosion. Some general advice can be given for operation on gas:
- Use cylinder oils with good deposit control to avoid deposit build up.
- Cylinder oil feed rates should be kept as low as possible.
- Lubricant oil quills or injectors must be kept in good working order to maintain correct oil dosing and distribution.
- Drains (scavenge air, water mist catcher, receiver, and piston underside) must be kept clean and fully operational.
- Cylinder condition should be monitored, and action should be taken based on observations. As wear is generally low, actions to address deposit build-up should be the priority.
Another widely discussed fuel, methanol, has been used as fuel in a number of vessels, that were partly lubricated with Chevron products. Regular scrapedown oil analysis using Chevron’s DOT.FAST service and frequent in-situ liner measurements were used to monitor cylinder condition. Cylinders reportedly appear much cleaner when burning methanol than conventional liquid fuels.
Engine makers’ approaches
Engine maker MAN Energy Solutions already has two-stroke marine engines operating on LNG, methanol, ethane and LPG. According the company’s research department, lubrication requirements remain consistent across these fuels. »In all cases [except the forthcoming low-pressure ME-GA dual-fuel LNG engine] our engines use the Diesel process, so the concept of what is needed from the lubricant is similar. For all low-sulphur fuels the recommendations are essentially the same as for 0.10 % and <0.50 % sulphur fuels,« an MAN spokesperson is cited.
MAN ES also recommends cermet piston ring coating for all engines running on low-sulphur fuels, in order to increase the margin against damage to the piston rings and cylinder liners. Svensson also notes that lubrication recommendations can change as MAN ES learns more about how engines operate with these new fuels, and as engines get updated.
MAN ES also notes the distinction between fuels currently in use and another future fuel candidate — ammonia. An ammonia engine is under development and is expected to be available commercially by 2024. It is too early to describe cylinder condition concept or lubrication requirements for this new engine type.
Engine developer WinGD designs two-stroke engines that include a low-pressure, Otto-cycle dual-fuel engine capable of running on LNG and fuel oil. This engine concept in particular offers the potential for future fuel flexibility, although its Diesel-process engines will also be candidates for running on liquid future fuels. According to WinGD, the current tribology concept works for both liquid and gaseous fuels. However, detailed lubricant requirements cannot be confirmed until more testing of future fuels have been carried out.
New engines adding complexity
New fuel types might have different combustion concepts as well as different fuel properties and different combustion by-products. The impact of new fuels is just one element of future cylinder condition. Arguably more important is the impact of engine advances to further increase fuel efficiency.
Fuel efficiency will help ship operators minimise emissions until lower-carbon fuels are widely available. And once running on those fuels, which could come at a significant premium compared to today’s fuels, efficient engines will help to keep costs manageable. The major avenue for increasing fuel efficiency in two-stroke engines is through increasing combustion pressure. This can have an impact on cylinder cleanliness if the lubricant is not sufficiently resistant to higher temperatures. For future cylinder oils, increasing thermal stability and reducing the potential for forming deposits in cylinders will be crucial.
The Otto-cycle concept of compressing a fuel-air mix and then igniting it — as opposed to the Diesel process of igniting fuel as it is injected — means that lower deposits are even more important. »Because you are igniting a mix with a pilot fuel, any other sort of ignition will also ignite the mixture — say a glowing piece of deposit on the piston crown. This means you can get uncontrolled combustion. The calcium carbonate or metals in general from cylinder oil additives will not help you at all. So, we believe that lower ash products are required«, a Chevron expert states.
Lower ash products will be needed not just for low-pressure Otto engines, but for future low-pressure engine designs using other fuels. There will also be a need among engines using exhaust gas after-treatment such as selective catalytic reduction (SCR) and particulate filters to lower emissions such as Nox and particulate matter, respectively. After-treatment is likely to become a more important element of many marine engines — whether to remove sulphur, to lower NOx (selective catalytic reduction or exhaust gas recirculation), to reduce methane slip or to minimise particulate emissions (diesel particulate filters) in line with potential future regulation.
The presence of after-treatment in the post-combustion chain means that engines will have to work harder to expel exhaust, which could lead to less complete scavenging. This means more combustion by-products would likely remain in the engine cylinder. If those by-products include ash from the metallic elements in lubricants, this could lead to more deposits in the cylinder. Even if ash deposits are not problematic in the cylinder, the fouling that ash can cause along the post-combustion chain means that it should be minimised, especially where after-treatment is deployed. (The Whitepaper can be downloaded from https://www.chevronmarineproducts.com/) RD